Universal joint fork lug side face milling clamp
A universal joint fork and milling lug technology, which is applied to the field of the side fixture of the universal joint fork milling lug, can solve the problems of lack of positioning support, slow speed, inability to meet high efficiency and speed, and achieves good effect, high efficiency and simple structure. Effect
- Summary
- Abstract
- Description
- Claims
- Application Information
AI Technical Summary
Problems solved by technology
Method used
Image
Examples
Embodiment 1
[0019] like figure 1 , figure 2 As shown, a universal joint fork milling ear side fixture, it includes hydraulic cylinder 1, hexagonal bolt 2, hinge fork seat A3, pin shaft B4, hinge fork seat B7, hydraulic three-jaw chuck 8, intermediate transition Disk 9, hexagon socket head screw A10, pin shaft A12, positioning pin 13, cotter pin 14, hexagon socket head screw B15, cylindrical pin 16, hexagon socket head screw C17, hexagon socket head screw D18, the hydraulic cylinder 1 is fixed Set on the base 11, the joint between the hydraulic cylinder 1 and the base 11 is provided with a hexagonal bolt 2, and the power output end of the hydraulic cylinder 1 is connected to the connecting rod 6 through the hinge fork seat A3; the connecting rod 6 The middle section of the connecting rod 6 is hinged on the base 11 through the pin shaft B4, one end of the connecting rod 6 is connected to the hydraulic cylinder 1 through the hinge fork A3, and the other end of the connecting rod 6 is conne...
Embodiment 2
[0025] like figure 1 , figure 2As shown, a universal joint fork milling ear side fixture, it includes hydraulic cylinder 1, hexagonal bolt 2, hinge fork seat A3, pin shaft B4, hinge fork seat B7, hydraulic three-jaw chuck 8, intermediate transition Disk 9, hexagon socket head screw A10, pin shaft A12, positioning pin 13, cotter pin 14, hexagon socket head screw B15, cylindrical pin 16, hexagon socket head screw C17, hexagon socket head screw D18, the hydraulic cylinder 1 is fixed Set on the base 11, the joint between the hydraulic cylinder 1 and the base 11 is provided with a hexagonal bolt 2, and the power output end of the hydraulic cylinder 1 is connected to the connecting rod 6 through the hinge fork seat A3; the connecting rod 6 The middle section of the connecting rod 6 is hinged on the base 11 through the pin shaft B4, one end of the connecting rod 6 is connected to the hydraulic cylinder 1 through the hinge fork A3, and the other end of the connecting rod 6 is connec...
PUM
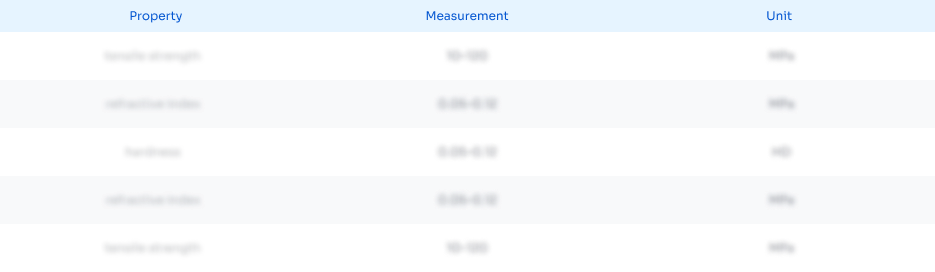
Abstract
Description
Claims
Application Information

- R&D
- Intellectual Property
- Life Sciences
- Materials
- Tech Scout
- Unparalleled Data Quality
- Higher Quality Content
- 60% Fewer Hallucinations
Browse by: Latest US Patents, China's latest patents, Technical Efficacy Thesaurus, Application Domain, Technology Topic, Popular Technical Reports.
© 2025 PatSnap. All rights reserved.Legal|Privacy policy|Modern Slavery Act Transparency Statement|Sitemap|About US| Contact US: help@patsnap.com