Stable nitrogen-doped carbon nanotube and iron oxide composite anode material and preparation method thereof
A nitrogen-doped carbon and negative electrode material technology, applied in battery electrodes, electrochemical generators, electrical components, etc., can solve the problems of poor cycle performance and drastic volume changes, and achieve improved rate performance, simple preparation process, and improved pumping. The effect of sub-charge and discharge efficiency
- Summary
- Abstract
- Description
- Claims
- Application Information
AI Technical Summary
Problems solved by technology
Method used
Image
Examples
Embodiment 1
[0032] Embodiment 1: with FeCl 3 Preparation of 10% Fe for iron source 2 o 3 / NCNTs composite material as an example
[0033] First, weigh 5 g of FeCl 3 ·6H 2 O was put into a beaker, added 20 milliliters of deionized water, stirred and dissolved to obtain FeCl 3 solution. Next, add 250ml of deionized water into a 500ml beaker, and move to an oil bath to boil. Then, under stirring, the FeCl 3 The solution was added dropwise to the above boiling liquid until a reddish-brown colloid appeared, then stopped heating and stirring. Dialyze the above-mentioned colloid through a semi-permeable membrane and transfer it into a beaker. Under stirring, add a slurry with a solid content of 50% nitrogen-doped carbon nanotubes of 12.87 grams, continue stirring for 10 hours, and then place it in an oven for drying after 10 hours of ultrasonic treatment. . Finally, the dried sample was treated at 500°C for 5 hours under an Ar flow of 100 sccm, and then cooled to obtain 40% Fe 2 o 3 / ...
Embodiment 2
[0034] Embodiment 2: with FeCl 3 Preparation of 40% Fe for iron source 2 o 3 / NCNTs composite material as an example
[0035] First, weigh 5 g of FeCl 3 ·6H 2O was put into a beaker, added 20 milliliters of deionized water, stirred and dissolved to obtain FeCl 3 solution. Next, add 250ml of deionized water into a 500ml beaker, and move to an oil bath to boil. Then, under stirring, the FeCl 3 The solution was added dropwise to the above boiling liquid until a reddish-brown colloid appeared, then stopped heating and stirring. Dialyze the above colloid through a semi-permeable membrane and move it into a beaker. Under stirring, add a slurry with a solid content of 50% nitrogen-doped carbon nanotubes of 2.144 grams, continue stirring for 10 hours and then ultrasonically treat it for 10 hours, then place it in an oven for drying . Finally, the dried sample was treated at 500°C for 5 hours under an Ar flow of 100 sccm, and then cooled to obtain 40% Fe 2 o 3 / NCNTs composi...
Embodiment 3
[0036] Embodiment 3: with FeCl 3 Preparation of 50% Fe for iron source 2 o 3 / NCNTs composite material as an example
[0037] First, weigh 5 g of FeCl 3 ·6H 2 O was put into a beaker, added 20 milliliters of deionized water, stirred and dissolved to obtain FeCl 3 solution. Next, add 250ml of deionized water into a 500ml beaker, and move to an oil bath to boil. Then, under stirring, the FeCl 3 The solution was added dropwise to the above boiling liquid until a reddish-brown colloid appeared, then stopped heating and stirring. Dialyze the above-mentioned colloid through a semi-permeable membrane and move it into a beaker. Under stirring, add a slurry with a solid content of 50% nitrogen-doped carbon nanotubes of 1.43 grams, continue stirring for 10 hours, and then place it in an oven for drying after 10 hours of ultrasonic treatment. . Finally, the dried sample was treated at 500°C for 5 h under 100 sccm Ar flow and then cooled to obtain 50% Fe 2 o 3 / NCNTs composites...
PUM
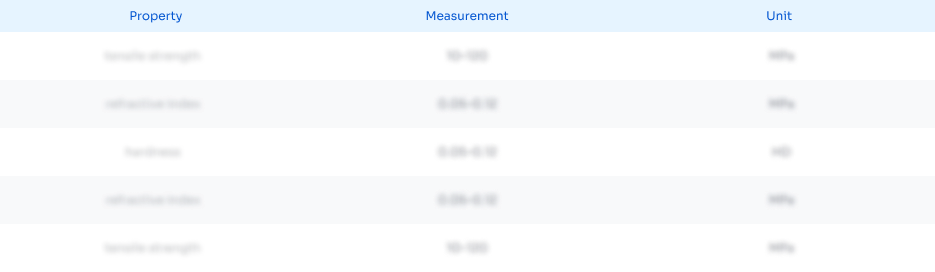
Abstract
Description
Claims
Application Information

- R&D
- Intellectual Property
- Life Sciences
- Materials
- Tech Scout
- Unparalleled Data Quality
- Higher Quality Content
- 60% Fewer Hallucinations
Browse by: Latest US Patents, China's latest patents, Technical Efficacy Thesaurus, Application Domain, Technology Topic, Popular Technical Reports.
© 2025 PatSnap. All rights reserved.Legal|Privacy policy|Modern Slavery Act Transparency Statement|Sitemap|About US| Contact US: help@patsnap.com