System capable of utilizing smoke waste heat in gradient mode for assisting in removing SO3 and improving dust removing efficiency
A flue gas waste heat and cascade technology, applied in the direction of reducing greenhouse gases, climate sustainability, lighting and heating equipment, etc., can solve the problems of decreased dust removal efficiency, low energy utilization efficiency, and high specific resistance of fly ash, etc., to achieve Achieve cascade utilization, improve dust removal efficiency, and reduce flue gas temperature
- Summary
- Abstract
- Description
- Claims
- Application Information
AI Technical Summary
Problems solved by technology
Method used
Image
Examples
Embodiment 1
[0038] like figure 1 As shown, this embodiment includes a boiler 1 , a denitration device 2 , an air preheater 3 , an electrostatic precipitator 4 , an induced draft fan 5 , a desulfurization absorption tower 6 and a chimney 7 sequentially connected along the flue at the tail of the boiler 1 . A first bypass is connected in parallel with the air preheater 3. The first bypass is connected to the second high-pressure heater 15 and the third high-pressure heater respectively through the regulating valve 20 and the connecting pipeline through the primary heat exchanger 8 and the secondary heat exchanger 9. The water inlet pipe and the water outlet pipe of the heater 16 are connected to form. Under the condition of high load of the unit, under the condition of poor coal quality, especially when the fuel of inferior quality such as lignite is used, and the amount of flue gas after the fuel is burned is greater than the designed amount of flue gas of air preheater 3, a part of the fl...
PUM
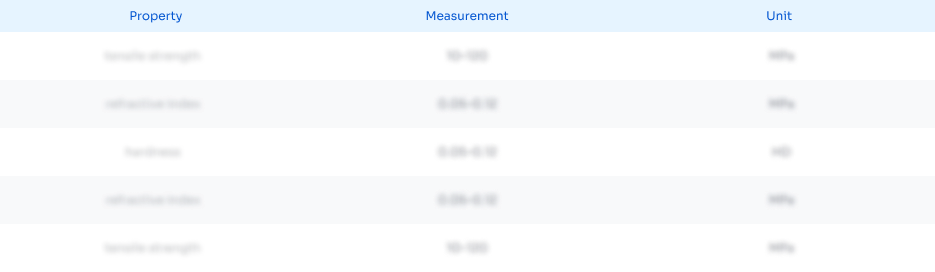
Abstract
Description
Claims
Application Information

- R&D Engineer
- R&D Manager
- IP Professional
- Industry Leading Data Capabilities
- Powerful AI technology
- Patent DNA Extraction
Browse by: Latest US Patents, China's latest patents, Technical Efficacy Thesaurus, Application Domain, Technology Topic, Popular Technical Reports.
© 2024 PatSnap. All rights reserved.Legal|Privacy policy|Modern Slavery Act Transparency Statement|Sitemap|About US| Contact US: help@patsnap.com