Superplastic forming mold design method based on finite element technique with consideration of thermal expansion
A superplastic forming and mold design technology, applied in the field of mechanical processing and forming simulation, can solve the problems of large deformation, not fully considering the forming error of parts, multi-layer structure, etc., and achieve the effect of improving the forming accuracy
- Summary
- Abstract
- Description
- Claims
- Application Information
AI Technical Summary
Problems solved by technology
Method used
Image
Examples
Embodiment Construction
[0030] See figure 1 — image 3 , which will be combined below figure 2 The schematic flow chart of the superplastic forming die design method further explains the design method of a superplastic forming die based on finite element technology considering thermal expansion in this patent application. It includes the following steps:
[0031] Step 1) Carry out the superplastic forming simulation in the finite element simulation software, and calculate and obtain the superplastic forming part.
[0032] Step 2) Using the thermal expansion properties of the part material, the thermal expansion simulation of the superplastic formed part obtained in step 1) is performed separately.
[0033] Step 3) Export the outer contour of the thermally expanded part obtained in step 2), and design the mold surface of the superplastic forming mold and the corresponding three-dimensional overall model of the mold according to the derived result in the three-dimensional modeling software.
[0034...
PUM
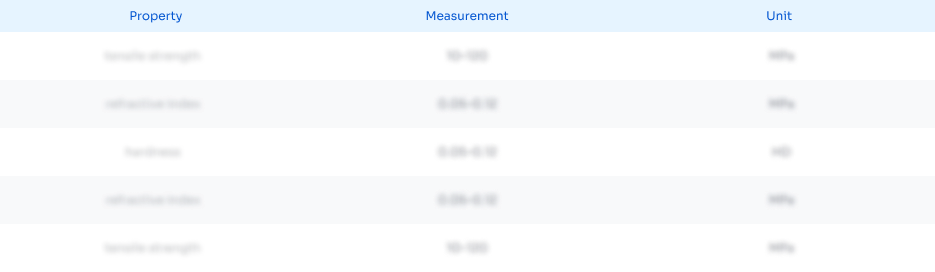
Abstract
Description
Claims
Application Information

- Generate Ideas
- Intellectual Property
- Life Sciences
- Materials
- Tech Scout
- Unparalleled Data Quality
- Higher Quality Content
- 60% Fewer Hallucinations
Browse by: Latest US Patents, China's latest patents, Technical Efficacy Thesaurus, Application Domain, Technology Topic, Popular Technical Reports.
© 2025 PatSnap. All rights reserved.Legal|Privacy policy|Modern Slavery Act Transparency Statement|Sitemap|About US| Contact US: help@patsnap.com