Continuous aluminum magnesium alloy thermal treatment furnace
An aluminum-magnesium alloy and heat treatment furnace technology, applied in heat treatment furnaces, heat treatment equipment, furnaces, etc., can solve the problems of consuming large man-hours, increasing space waste, increasing resource consumption, etc., and achieves high automation, stable operation, and heat treatment efficiency high effect
- Summary
- Abstract
- Description
- Claims
- Application Information
AI Technical Summary
Problems solved by technology
Method used
Image
Examples
Embodiment 1
[0028] figure 1 It is a schematic diagram of the overall structure of an aluminum-magnesium alloy heat treatment furnace according to the embodiment of the present invention; figure 2 It is a top view of an aluminum-magnesium alloy heat treatment furnace according to the embodiment of the present invention; image 3 It is an internal gas flow diagram of an aluminum-magnesium alloy heat treatment furnace according to Embodiment 1 of the present invention. Such as figure 1 , figure 2 and image 3 As shown, a continuous aluminum-magnesium alloy heat treatment furnace includes a pretreatment chamber 1, a gas heating furnace 2, a cooling chamber 3, a puller 4, a material basket 5 and a gas heating unit 6, and the material basket 5 is used to place aluminum Magnesium alloy, characterized in that: the pretreatment chamber 1 and the cooling chamber 3 are placed at both ends of the gas heating furnace 2 and communicate with the gas heating furnace 2 respectively; the pretreatment...
PUM
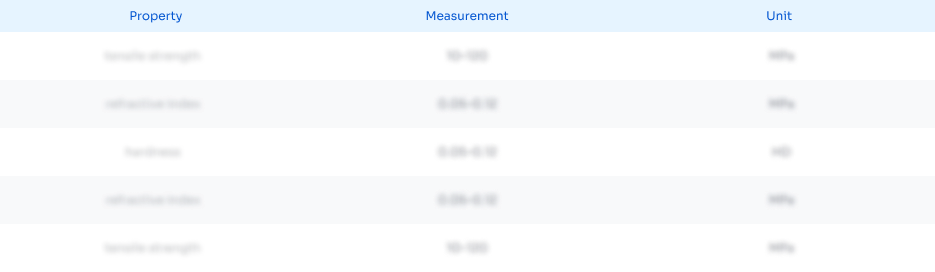
Abstract
Description
Claims
Application Information

- R&D
- Intellectual Property
- Life Sciences
- Materials
- Tech Scout
- Unparalleled Data Quality
- Higher Quality Content
- 60% Fewer Hallucinations
Browse by: Latest US Patents, China's latest patents, Technical Efficacy Thesaurus, Application Domain, Technology Topic, Popular Technical Reports.
© 2025 PatSnap. All rights reserved.Legal|Privacy policy|Modern Slavery Act Transparency Statement|Sitemap|About US| Contact US: help@patsnap.com