Glaze of brunet ceramic and preparation method of glaze
A technology of glaze and ceramics, applied in the field of ceramics, can solve the problems of low quality rate of ceramic products, influence of product quality, increase of production cost, etc., achieve the effect of controlling white spots and improving the rate of excellence
- Summary
- Abstract
- Description
- Claims
- Application Information
AI Technical Summary
Problems solved by technology
Method used
Image
Examples
Embodiment 1
[0020] Embodiment one, the ratio of bottom glaze and transparent glaze is respectively 90% and 10%.
[0021] The bottom glaze is composed of the following raw materials in parts by weight: 3 parts of ultra-white zirconium silicate, 20 parts of ordinary potassium feldspar powder, 25 parts of albite feldspar, 4 parts of alumina, 9 parts of kaolin and 6 parts of calcined kaolin. The transparent glaze is composed of the following raw materials in parts by weight: 3 parts of calcined zinc oxide, 9 parts of barium carbonate, 30 parts of albite, 0 part of calcined alumina, 13 parts of calcite, 9 parts of calcite, 5 parts of quartz, and 9 parts of kaolin Composed of 12 parts of calcined kaolin.
[0022] Carry out the weighing ratio mixing of raw materials according to the above ratio.
Embodiment 2
[0024] The bottom glaze is composed of the following raw materials in parts by weight: 3 parts of ultra-white zirconium silicate, 20 parts of ordinary potassium feldspar powder, 25 parts of albite feldspar, 4 parts of alumina, 9 parts of kaolin and 6 parts of calcined kaolin. The transparent glaze is composed of the following raw materials in parts by weight: 5 parts of calcined zinc oxide, 7 parts of barium carbonate, 30 parts of potassium feldspar powder, 0.5 parts of calcined alumina, 12 parts of calcite, 10 parts of calcite, 5 parts of quartz, and 9 parts of kaolin Composed of 7 parts of calcined kaolin. The quartz is finely ground quartz after being screened with 325 meshes.
[0025] Carry out the weighing ratio mixing of raw materials according to the above ratio.
Embodiment 3
[0027] The bottom glaze is composed of the following raw materials in parts by weight: 3 parts of ultra-white zirconium silicate, 20 parts of ordinary potassium feldspar powder, 25 parts of albite feldspar, 4 parts of alumina, 9 parts of kaolin and 6 parts of calcined kaolin. The transparent glaze is composed of the following raw materials in parts by weight: 5 parts of burnt zinc oxide, 7 parts of barium carbonate, 30 parts of potassium feldspar powder, 2 parts of calcined alumina, 12 parts of burnt talc, 10 parts of calcite, 5 parts of quartz, and 9 parts of kaolin Composed of 14 parts of calcined kaolin. The quartz is finely ground quartz after being screened with 325 meshes.
[0028] Carry out the weighing ratio mixing of raw materials according to the above ratio.
[0029] In addition, the present invention also discloses a preparation method of a dark ceramic glaze, comprising the following steps:
[0030] 1) Weigh the raw materials according to the weight components o...
PUM
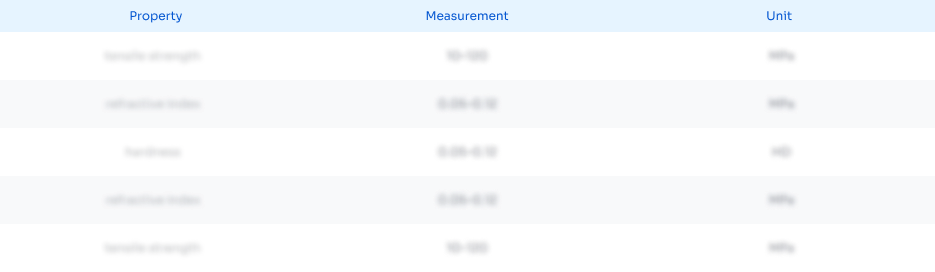
Abstract
Description
Claims
Application Information

- R&D
- Intellectual Property
- Life Sciences
- Materials
- Tech Scout
- Unparalleled Data Quality
- Higher Quality Content
- 60% Fewer Hallucinations
Browse by: Latest US Patents, China's latest patents, Technical Efficacy Thesaurus, Application Domain, Technology Topic, Popular Technical Reports.
© 2025 PatSnap. All rights reserved.Legal|Privacy policy|Modern Slavery Act Transparency Statement|Sitemap|About US| Contact US: help@patsnap.com