Single-man manual-control rotorcraft
A gyrocopter and manual control technology, which is applied in the field of aircraft, can solve the problems of troublesome maintenance, difficult adaptation, and large production cost.
- Summary
- Abstract
- Description
- Claims
- Application Information
AI Technical Summary
Problems solved by technology
Method used
Image
Examples
Embodiment 1
[0140] Embodiment one: if figure 1 , figure 2 As shown, the single-person manual rotorcraft of the present invention is composed of a fuselage part, a rotor shaft cantilever tilting structure, a full manual control mechanism, and an internal variable-distance rotor head mechanism. The wheel is directly in front, the tail is placed at the rear, the driver's seat and the engine are respectively placed at the front and rear of the column, the propeller is used as the power, and the three-point frame type independent shock-absorbing support mechanism with the propeller reaction force balance device is used to balance the air force when the propeller is working. The reaction force generated by the fuselage increases the stability of the whole machine itself. Through the full manual control mechanism with steering connection function, the driver can complete the rotor pitch change, rotor shaft tilt, Full manual operation of flight steering and brakes.
[0141] Such as figure 2 ...
Embodiment 2
[0142] Embodiment two: if image 3 , Figure 4 , Figure 5 As shown, the fuselage part of the single hand-controlled rotorcraft of this embodiment is mainly composed of two parts, the fuselage main support and the three-point frame type independent shock-absorbing support mechanism with the propeller reaction force balance device.
[0143] Such as image 3 As shown, the fuselage main support adopts the positive three-point landing gear fuselage with a high center of gravity, adopts a front steering wheel 17 to be placed in the front, and is formed by the front horizontal support rod 33, the rear horizontal support rod 34, and the lateral support rod 35 through the middle two sides. And the three-point frame type independent shock-absorbing support mechanism that left and right support wheels 16 form is used as lateral support, and the lateral support bar 35 support of its both sides is connected on the upper steering joint base 108 both sides on the upper position of column ...
Embodiment 3
[0147] Embodiment three: as Image 6 , Figure 7 As shown, the rotor head mechanism of the single hand-controlled rotorcraft of this embodiment is composed of three parts: a splint-type propeller hub mechanism with internal variable pitch, a main structure of the rotor shaft, and a rotor connection and installation part.
[0148] Such as Image 6 As shown, the upper propeller hub surface 53 and the lower propeller hub surface 54 are two symmetrical elongated splints, the periphery of the two is provided with corresponding bolt connection holes, and the center of the two is processed with a vertically penetrating double-row ball The mounting hole of the bearing 55 is centered on the mounting hole of the double-row ball bearing 55, along the center line of the upper paddle hub surface 53 and the lower paddle hub surface 54 toward each end, each corresponding to a vertically penetrating upper paddle hub surface 53 and the mounting hole of the variable pitch joint bearing 56 on ...
PUM
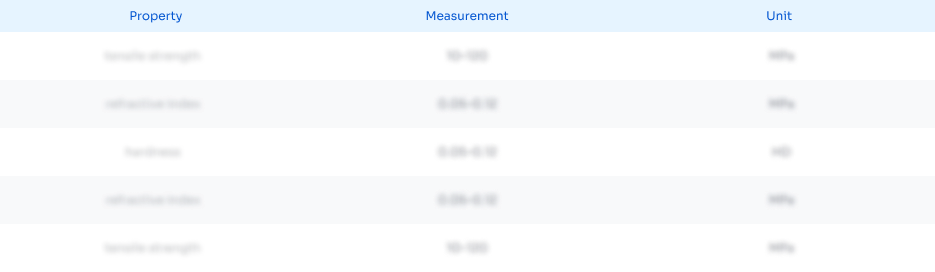
Abstract
Description
Claims
Application Information

- R&D
- Intellectual Property
- Life Sciences
- Materials
- Tech Scout
- Unparalleled Data Quality
- Higher Quality Content
- 60% Fewer Hallucinations
Browse by: Latest US Patents, China's latest patents, Technical Efficacy Thesaurus, Application Domain, Technology Topic, Popular Technical Reports.
© 2025 PatSnap. All rights reserved.Legal|Privacy policy|Modern Slavery Act Transparency Statement|Sitemap|About US| Contact US: help@patsnap.com