Metal melting method
A metal and melting technology, applied in the direction of preheating, waste heat treatment, energy industry, etc., can solve the problems of discontinuity, laborious pouring of liquid metal, and danger, and achieve a high degree of safety.
- Summary
- Abstract
- Description
- Claims
- Application Information
AI Technical Summary
Problems solved by technology
Method used
Examples
Embodiment Construction
[0010] In order to achieve the above-mentioned object of the invention, the technical means used in the present invention is to make a metal melting furnace include: a heating furnace, in which a heating chamber is formed; a melting furnace, which is erected on the heating furnace, and the melting furnace includes a furnace body And a cover plate, the furnace body is placed in the heating chamber of the heating furnace, and the cover plate covers the top surface of the furnace body to close the furnace body; a regenerative combustion system includes a regenerator, at least one For the burner, at least a pair of regenerators, and at least one exhaust pipe, the regenerator is in communication with the heating chamber, the burner is arranged in the regenerator, and the heating chamber of the heating furnace is alternately performed Heating, the heat storage body is respectively arranged on the combustor, the intake end of one end of the exhaust pipe is connected to the combustor, a...
PUM
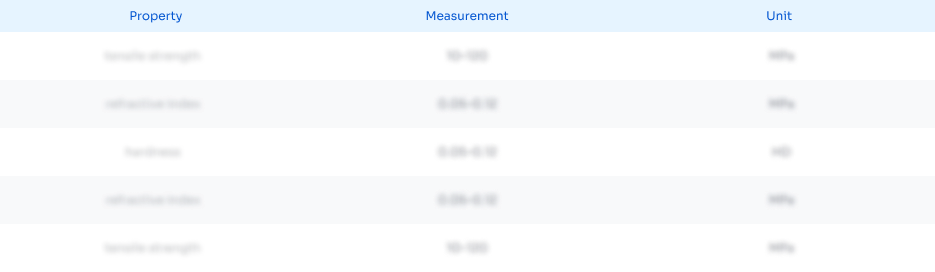
Abstract
Description
Claims
Application Information

- R&D
- Intellectual Property
- Life Sciences
- Materials
- Tech Scout
- Unparalleled Data Quality
- Higher Quality Content
- 60% Fewer Hallucinations
Browse by: Latest US Patents, China's latest patents, Technical Efficacy Thesaurus, Application Domain, Technology Topic, Popular Technical Reports.
© 2025 PatSnap. All rights reserved.Legal|Privacy policy|Modern Slavery Act Transparency Statement|Sitemap|About US| Contact US: help@patsnap.com