Lithium separation material preparation method
A technology for separating materials and dispersants, applied in chemical instruments and methods, other chemical processes, etc., can solve the problems of lithium ion loss, adsorption capacity limitation, etc., and achieve the effect of improving adsorption capacity, not easy to be lost, and high adsorption capacity
- Summary
- Abstract
- Description
- Claims
- Application Information
AI Technical Summary
Problems solved by technology
Method used
Image
Examples
Embodiment 1
[0024] Step 1. Preparation of water phase
[0025] In parts by weight, add 100 parts of pure water and 0.5 part of gelatin into the reactor, and stir evenly.
[0026] Step 2. Preparation of oil phase
[0027] Mix and stir the oil phase components in the following proportions evenly;
[0028]
[0029]
[0030] Step 3. Suspension Polymerization
[0031] Add the prepared oil phase solution in step 2 to the reaction kettle equipped with the prepared water phase in step 1, react at 90°C for 14 hours, discharge the material after the reaction is completed, and extract the porogen after drying to obtain product. The number is W-1.
Embodiment 2
[0033] Step 1. Preparation of water phase
[0034] In parts by weight, add 100 parts of pure water and 1.5 parts of polyvinyl alcohol into the reactor, and stir evenly.
[0035] Step 2. Preparation of oil phase
[0036] Mix and stir the oil phase components in the following proportions evenly;
[0037]
[0038] Step 3. Suspension Polymerization
[0039] Add the prepared oil phase solution to the reaction kettle equipped with the prepared water phase in step 1, react at 80°C for 24 hours, discharge the material after the reaction is completed, and extract the porogen after drying to obtain the product, No. for W-2.
Embodiment 3
[0041] Step 1. Preparation of water phase
[0042] In parts by weight, add 100 parts of pure water and 2 parts of hydroxymethylcellulose into the reactor, and stir evenly.
[0043] Step 2. Preparation of oil phase
[0044] Mix and stir the oil phase components in the following proportions evenly;
[0045]
[0046] Step 3. Suspension Polymerization
[0047] Add the prepared oil phase solution to the reaction kettle equipped with the prepared water phase in step 1, react at 110°C for 10 hours, discharge the material after the reaction is completed, and extract the porogen after drying to obtain the product, No. for W-3.
PUM
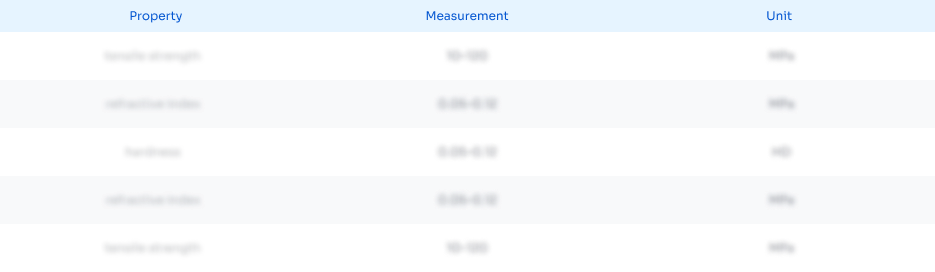
Abstract
Description
Claims
Application Information

- R&D
- Intellectual Property
- Life Sciences
- Materials
- Tech Scout
- Unparalleled Data Quality
- Higher Quality Content
- 60% Fewer Hallucinations
Browse by: Latest US Patents, China's latest patents, Technical Efficacy Thesaurus, Application Domain, Technology Topic, Popular Technical Reports.
© 2025 PatSnap. All rights reserved.Legal|Privacy policy|Modern Slavery Act Transparency Statement|Sitemap|About US| Contact US: help@patsnap.com