Fault detecting method for rail pressure sensor in common rail system
A technology of rail pressure sensor and common rail system, applied in machine/engine, fuel injection control, engine control, etc., can solve problems such as undetectable drift, incomplete fault phenomenon, inappropriate selection of reference objects, etc.
- Summary
- Abstract
- Description
- Claims
- Application Information
AI Technical Summary
Problems solved by technology
Method used
Image
Examples
Embodiment Construction
[0018] The present invention will be further described below in conjunction with drawings and embodiments.
[0019] At present, more and more programs are replacing the previous mechanical pressure limiting valves with electronic pressure limiting valves. The solution of the present invention is to use the electronic pressure limiting valve to control the rail pressure, compare the sampled value of the rail pressure sensor with the control pressure of the electronic pressure limiting valve, and diagnose the rail pressure sensor.
[0020] figure 1 A structural diagram of a fuel system implementing the present invention is shown. The fuel delivery pump 5 delivers fuel from the fuel tank 1 to the high-pressure pump 7 through the low-pressure fuel pipe 3 and the filter 4. The fuel inlet valve 6 controls the fuel flow into the high-pressure pump. The fuel is pressurized by the high-pressure pump 7 and stored in the high-pressure rail pipe 10 Among them, the fuel injector 12 is c...
PUM
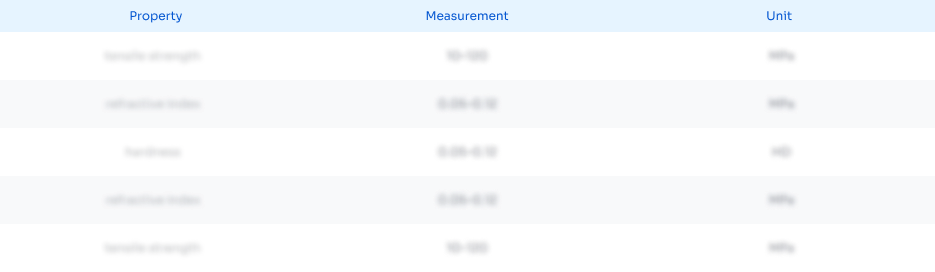
Abstract
Description
Claims
Application Information

- R&D
- Intellectual Property
- Life Sciences
- Materials
- Tech Scout
- Unparalleled Data Quality
- Higher Quality Content
- 60% Fewer Hallucinations
Browse by: Latest US Patents, China's latest patents, Technical Efficacy Thesaurus, Application Domain, Technology Topic, Popular Technical Reports.
© 2025 PatSnap. All rights reserved.Legal|Privacy policy|Modern Slavery Act Transparency Statement|Sitemap|About US| Contact US: help@patsnap.com