Drill hole layout method for gas extraction during primary mining and stoping of large mining height fully-mechanized face
A technology for fully mechanized mining face and gas drainage, which is used in gas discharge, safety devices, mining equipment, etc., and can solve the problem of high drilling failure, pressure relief gas flow, and large gas flow in goafs, etc. problems, to achieve the effect of improving the extraction volume and utilization rate, reducing the amount of gas gushing, and ensuring production safety.
- Summary
- Abstract
- Description
- Claims
- Application Information
AI Technical Summary
Problems solved by technology
Method used
Image
Examples
Embodiment Construction
[0031] The roadway layout of fully mechanized mining face with large mining height is as follows: figure 1 As shown, it is generally arranged as a "three-inlet and two-return" ventilation system. The entire coal mining area is composed of five roadways, gas return airways, and cutouts.
[0032] The specific implementation of the low-level drilling: the low-level drilling is relatively short, and ordinary drilling rigs are used to drill holes from the special gas return airway to the roof of the cutout. 6±1m, 30±2m in length, and 10~20m between adjacent low-level drill holes. Such as figure 2 and image 3 shown.
[0033] The specific implementation method of the middle drilling: use the 1000-meter directional drilling machine to construct the middle drilling at the appropriate position in the roadway on the return air side. The hole layers are arranged within the range of 6~25m from the coal seam roof (directly above the roof, below the old roof), and in the lateral direct...
PUM
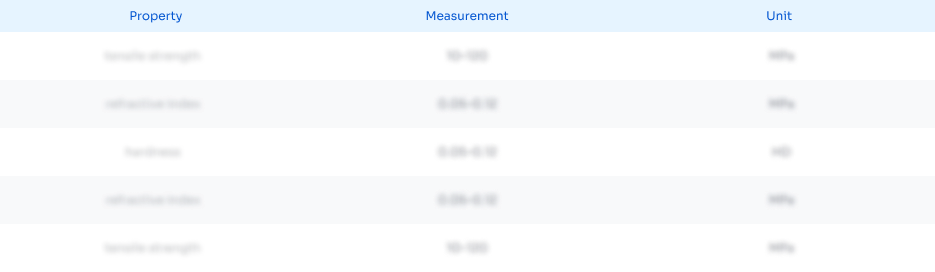
Abstract
Description
Claims
Application Information

- R&D
- Intellectual Property
- Life Sciences
- Materials
- Tech Scout
- Unparalleled Data Quality
- Higher Quality Content
- 60% Fewer Hallucinations
Browse by: Latest US Patents, China's latest patents, Technical Efficacy Thesaurus, Application Domain, Technology Topic, Popular Technical Reports.
© 2025 PatSnap. All rights reserved.Legal|Privacy policy|Modern Slavery Act Transparency Statement|Sitemap|About US| Contact US: help@patsnap.com