Cooling system and method for spray forming of silicon-aluminum alloy
A technology of silicon-aluminum alloy and spray forming, which is applied in the field of cooling system, can solve the problems of low cooling efficiency and direct cooling of the deposition surface, and achieve the effects of increasing solidification speed, cooling efficiency and applicability
- Summary
- Abstract
- Description
- Claims
- Application Information
AI Technical Summary
Problems solved by technology
Method used
Image
Examples
Embodiment Construction
[0028] The embodiment of the present invention will be described by taking the dual-nozzle scanning oblique spray forming process as an example.
[0029] like figure 1 and figure 2 As shown, the spray deposition device is composed of a deposition box 3, a deposition tray and its moving device 12, and a deposition chamber door 2. The deposition box 3 encloses a closed deposition chamber 1, and an exhaust port 21 is provided at the lower end of the deposition chamber to deposit The gas and overspray powder in the chamber are discharged. The deposition disk and its moving device 12 perform rotating and descending motions during injection molding production, and are sealed with the deposition box by a sealing device. Before production, the deposition chamber door 2 is closed, and the deposition chamber 3 is sealed with a sealing strip. figure 1 Also shown is the deposited ingot 5 produced after a period of time, with the upper end being the deposition surface.
[0030] like ...
PUM
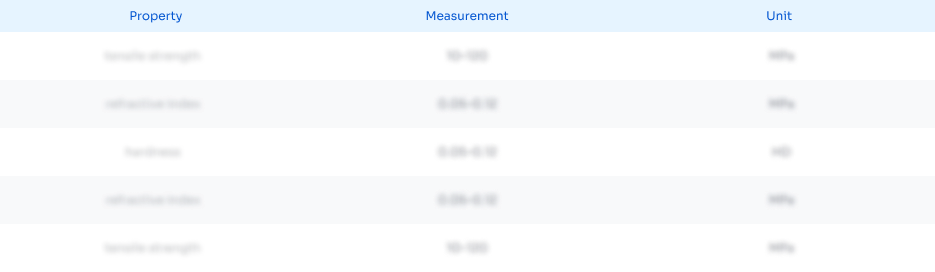
Abstract
Description
Claims
Application Information

- R&D
- Intellectual Property
- Life Sciences
- Materials
- Tech Scout
- Unparalleled Data Quality
- Higher Quality Content
- 60% Fewer Hallucinations
Browse by: Latest US Patents, China's latest patents, Technical Efficacy Thesaurus, Application Domain, Technology Topic, Popular Technical Reports.
© 2025 PatSnap. All rights reserved.Legal|Privacy policy|Modern Slavery Act Transparency Statement|Sitemap|About US| Contact US: help@patsnap.com