Multi-speed tail-drying-type mixed fertilizer granulation production process and special production equipment thereof
A technology of mixed fertilizer and production process, which is applied in the direction of fertilizer mixture, application, fertilization device, etc. It can solve the problems of lower yield and quality of finished product, inability to adjust residence time, and loose particles of finished product, so as to reduce the probability of agglomeration and benefit Promote the use, the effect of high roundness
- Summary
- Abstract
- Description
- Claims
- Application Information
AI Technical Summary
Problems solved by technology
Method used
Image
Examples
Embodiment Construction
[0011] Now refer to the attached figure 1 , the description is as follows in conjunction with the examples: The granulation production process of the multi-stage variable-speed end-drying mixed fertilizer according to the present invention: the raw materials enter the crusher after being premixed and stirred by the batching system, and enter the rotary fertilizer after being crushed, stirred and measured by the crusher. The drum granulator performs the first granulation, stay in the drum granulator for 5 to 9 minutes, the moisture content is 30% to 50%, the ball forming rate is 25% to 40%, and the granule temperature is 50 to 70 degrees; Then enter the disc granulator for secondary granulation, stay in the disc granulator for 2 to 3 minutes, the moisture content is 30% to 50%, the ball forming rate is 60% to 80%, and the temperature is 50 to 70 Then enter the suction-type primary drying drum for low-temperature drying, stay for 17 to 23 minutes, the moisture content is 25% to ...
PUM
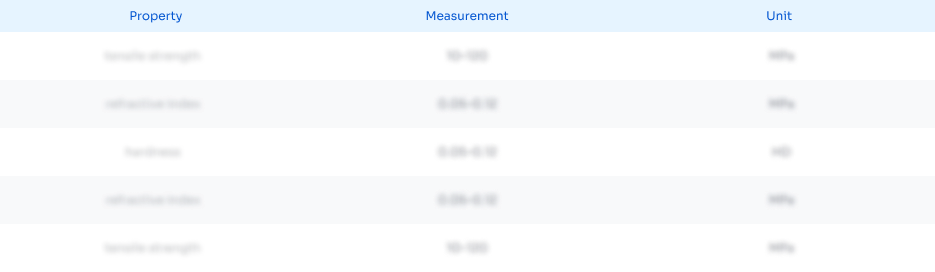
Abstract
Description
Claims
Application Information

- Generate Ideas
- Intellectual Property
- Life Sciences
- Materials
- Tech Scout
- Unparalleled Data Quality
- Higher Quality Content
- 60% Fewer Hallucinations
Browse by: Latest US Patents, China's latest patents, Technical Efficacy Thesaurus, Application Domain, Technology Topic, Popular Technical Reports.
© 2025 PatSnap. All rights reserved.Legal|Privacy policy|Modern Slavery Act Transparency Statement|Sitemap|About US| Contact US: help@patsnap.com