Chamfered crystallizer narrow-surface copper plate
A technology of chamfering crystallizers and narrow-faced copper plates, which is applied in the field of metal solidification and continuous casting, can solve problems such as processing costs and safety hindering crystallizers, affecting logistics and contract order delivery dates, and hindering the rapid development of crystallizers. Easy to clean and maintain, conducive to uniform growth, simple structure effect
- Summary
- Abstract
- Description
- Claims
- Application Information
AI Technical Summary
Problems solved by technology
Method used
Image
Examples
Embodiment 1
[0034] Embodiment 1: as figure 1 , 2, 3, a chamfering crystallizer narrow-faced copper plate, including a large surface area 3 and a side chamfering area 2, the back of the large surface area and the side chamfering are provided with one or more cooling water tanks that penetrate up and down, so The longitudinal sectional view of the working face in the large area is in the shape of a broken line. The broken line shape is composed of a first broken line and a vertical line. The included angle between the first fold line and the side of the narrow copper plate 1 is 6 degrees. The length of the first fold line is 22% of the crystallizer height. Angle a is the angle between the working surface of the chamfering area on the side of the vertical line and the side of the narrow copper plate. The angle a1 is the angle between the working surface of the chamfering area on the side of the first fold line and the side of the narrow copper plate. The chamfering angle a of the side c...
Embodiment 2
[0035] Embodiment 2: as figure 1 , 2 , 3, a chamfering crystallizer narrow-faced copper plate, including a large surface area 3 and a side chamfering area 2, the back of the large surface area and the side chamfering are provided with one or more cooling water tanks that penetrate up and down, so The longitudinal sectional view of the working face in the large area is in the shape of a broken line. The broken line shape is composed of a first broken line and a vertical line, the angle between the first broken line and the side of the narrow copper plate 1 is 10 degrees, and the length of the first broken line is 31% of the crystallizer height, further , the angle a is the angle between the working surface of the side chamfering area of the vertical line and the side of the narrow copper plate, and the angle a1 is the angle between the working surface of the side chamfering area of the first fold line and the side of the narrow copper plate, said The chamfering angle a of...
Embodiment 3
[0036] Embodiment 3: as figure 1 , 2 , 3, a chamfering crystallizer narrow-faced copper plate, including a large surface area 3 and a side chamfering area 2, the back of the large surface area and the side chamfering are provided with one or more cooling water tanks that penetrate up and down, so The longitudinal sectional view of the working face in the large area is in the shape of a broken line. The broken line shape is composed of a first broken line and a vertical line. The included angle between the first fold line and the side of the narrow copper plate 1 is 7 degrees. The length of the first fold line is 27% of the crystallizer height. Angle a is the angle between the working surface of the chamfering area on the side of the vertical line and the side of the narrow copper plate. The angle a1 is the angle between the working surface of the chamfering area on the side of the first fold line and the side of the narrow copper plate. The chamfering angle a of the side ...
PUM
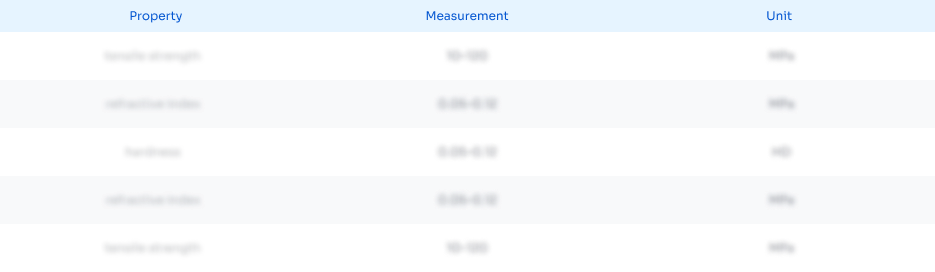
Abstract
Description
Claims
Application Information

- R&D
- Intellectual Property
- Life Sciences
- Materials
- Tech Scout
- Unparalleled Data Quality
- Higher Quality Content
- 60% Fewer Hallucinations
Browse by: Latest US Patents, China's latest patents, Technical Efficacy Thesaurus, Application Domain, Technology Topic, Popular Technical Reports.
© 2025 PatSnap. All rights reserved.Legal|Privacy policy|Modern Slavery Act Transparency Statement|Sitemap|About US| Contact US: help@patsnap.com