Nesting process machining method for off-axis reflection type optical part
A technology for optical parts and process processing, which is applied in the processing field of off-axis reflective optical parts, can solve problems such as impact, measurement error increase, manual repair high-frequency residual error, etc., and achieves wide adaptability, simple structure, and adaptability strong effect
- Summary
- Abstract
- Description
- Claims
- Application Information
AI Technical Summary
Problems solved by technology
Method used
Image
Examples
Embodiment Construction
[0028] The present invention will be described in further detail below in conjunction with the accompanying drawings.
[0029] figure 2 and image 3 It is an example of a special-shaped off-axis mirror structure as a processing object of an off-axis reflective optical part nesting process processing method of the present invention.
[0030] The specific steps of an off-axis reflective optical part nesting process processing method of the present invention are as follows:
[0031] 1. Measure the shape of off-axis aspheric optical parts, and leave a processing allowance for subsequent processes according to the processing technology;
[0032] 2. According to the measurement results of step 1, design and grind the nested master mirror. The so-called master mirror is the non-off-axis part of the off-axis mirror that is "completed", that is, it can be combined with the off-axis part to form a complete rotationally symmetrical area , the splicing gap between the mother mirror an...
PUM
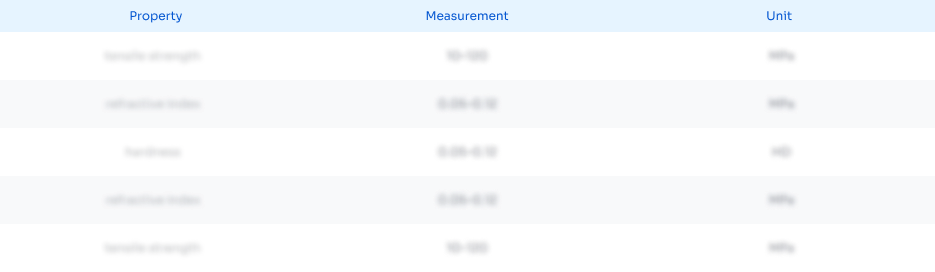
Abstract
Description
Claims
Application Information

- R&D Engineer
- R&D Manager
- IP Professional
- Industry Leading Data Capabilities
- Powerful AI technology
- Patent DNA Extraction
Browse by: Latest US Patents, China's latest patents, Technical Efficacy Thesaurus, Application Domain, Technology Topic, Popular Technical Reports.
© 2024 PatSnap. All rights reserved.Legal|Privacy policy|Modern Slavery Act Transparency Statement|Sitemap|About US| Contact US: help@patsnap.com