Yellow phosphorus tail gas purification method and system
A yellow phosphorus tail gas and purification system technology, which is applied in combustible gas purification, combustible gas purification/transformation, petroleum industry, etc., can solve problems such as boiler corrosion, high energy consumption, and poor purification effect, and achieve investment cost reduction and operation The effect of low energy consumption and low consumption
- Summary
- Abstract
- Description
- Claims
- Application Information
AI Technical Summary
Problems solved by technology
Method used
Image
Examples
Embodiment 1
[0021] The method for purifying yellow phosphorus tail gas of the present invention comprises the following steps: washing the yellow phosphorus tail gas with water at a temperature of 10° C. to remove dust and part of the phosphorus element; carrying out alkali washing on the washed yellow phosphorus tail gas to remove SO 2 、H 2 S and other acidic gases; the yellow phosphorus tail gas after alkali washing is oxidized in the first-stage oxidation solution to remove PH 3 , the first oxidation solution is KMnO 4 , the mass concentration of the first-stage oxidation solution is 0.8%; the oxidized yellow phosphorus tail gas is neutralized with NaOH solution to obtain the purified yellow phosphorus tail gas, and the mass concentration of the NaOH solution is 0.3%. The oxidized yellow phosphorus tail gas is subjected to a second oxidation treatment to remove residual pH 3 , the second oxidation solution used in the second oxidation treatment is KMnO 4 , the mass concentration of ...
Embodiment 2
[0028] The difference between this example and Example 1 is that the yellow phosphorus tail gas is washed with water at a temperature of 10°C to remove dust and some phosphorus elements; the washed yellow phosphorus tail gas is washed with alkali to remove SO 2 、H 2 S and other acidic gases; the yellow phosphorus tail gas after alkali washing is oxidized in the first-stage oxidation solution to remove PH 3 , the first oxidation solution is NaClO 3 , the mass concentration of the first-stage oxidation solution is 0.6%; the oxidized yellow phosphorus tail gas is neutralized with NaOH solution to obtain the purified yellow phosphorus tail gas, and the mass concentration of the NaOH solution is 0.6%. The oxidized yellow phosphorus tail gas is subjected to a second oxidation treatment to remove residual pH 3 , the second oxidation solution used in the second oxidation treatment is NaClO 3 , the mass concentration of the oxidation solution is 2%.
Embodiment 3
[0030] The difference between this example and Example 1 is that the yellow phosphorus tail gas is washed with water at a temperature of 15°C to remove dust and part of the phosphorus element; the washed yellow phosphorus tail gas is washed with alkali to remove SO 2 、H 2 S and other acidic gases; the yellow phosphorus tail gas after alkali washing is oxidized in the first-stage oxidation solution to remove PH 3 , the first oxidation solution is KClO 3 , the mass concentration of the first-stage oxidation solution is 0.6%; the oxidized yellow phosphorus tail gas is neutralized with NaOH solution to obtain the purified yellow phosphorus tail gas, and the mass concentration of the NaOH solution is 0.6%. The oxidized yellow phosphorus tail gas is subjected to a second oxidation treatment to remove residual pH 3 , the second oxidation solution used in the second oxidation treatment is KClO 3 , the mass concentration of the secondary oxidation solution is 2%.
PUM
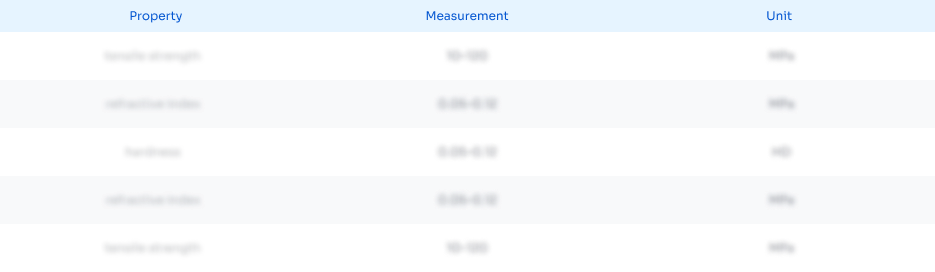
Abstract
Description
Claims
Application Information

- R&D
- Intellectual Property
- Life Sciences
- Materials
- Tech Scout
- Unparalleled Data Quality
- Higher Quality Content
- 60% Fewer Hallucinations
Browse by: Latest US Patents, China's latest patents, Technical Efficacy Thesaurus, Application Domain, Technology Topic, Popular Technical Reports.
© 2025 PatSnap. All rights reserved.Legal|Privacy policy|Modern Slavery Act Transparency Statement|Sitemap|About US| Contact US: help@patsnap.com