Hierarchically-controlled electromagnetic incremental forming method
A progressive forming and electromagnetic technology, which is applied in the field of parts forming and manufacturing, can solve problems such as instability and wrinkling, and achieve the effects of suppressing thinning, improving the precision of electromagnetic progressive forming, and smoothing the surface
- Summary
- Abstract
- Description
- Claims
- Application Information
AI Technical Summary
Problems solved by technology
Method used
Image
Examples
Embodiment 1
[0038] As shown in Figure 1, the specific implementation process of the example of the present invention is:
[0039] (1) Place the sheet material 1 to be formed on the first layer of the die 4 and press it with the binder ring 2; drive the forming coil 3 down until the forming coil 3 moves to the position where it is in contact with the sheet material 1 to be formed; Through charging and discharging, a pulse current is generated in the forming coil 3, and at the same time, an eddy current in the opposite direction is induced on the sheet 1 to be formed. Under the action of the Lorentz force, the sheet 1 to be formed deforms at a high speed.
[0040] The forming coil 3 located in the head of the progressive forming machine tool provides a power source for electromagnetic forming.
[0041] (2) After forming once, the forming coil 3 moves to a designated position according to a preset trajectory for the next discharge forming; and then moves to the next designated position for discharg...
Embodiment 2
[0050] Such as figure 2 It is a schematic diagram of the first layer before discharging. The method of forming the first layer can be one-time forming with a larger-sized coil, such as image 3 Shown. The large-sized forming coil 3 provides a large electromagnetic force range, which can form a large range at a time, but the cost is higher and the forming quality cannot be guaranteed. After the first layer is formed, the subsequent forming and orthopedic processes are continued.
Embodiment 3
[0052] The implementation method of the forming of the first layer may be multiple forming with a smaller-sized forming coil 3, such as Figure 4a , As shown in 4b. Figure 4a Is a schematic diagram of a discharge, Figure 4b In order to move the coil to the designated position for the second discharge after one discharge, the forming quality of sheet metal 1 can be improved by two or more discharges. After the first layer is formed, the subsequent forming and orthopedic processes are continued.
PUM
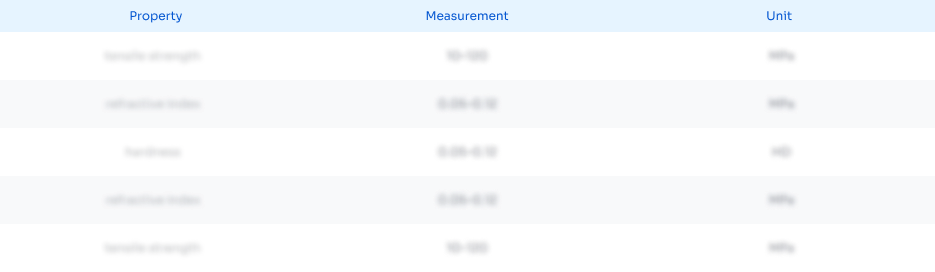
Abstract
Description
Claims
Application Information

- R&D
- Intellectual Property
- Life Sciences
- Materials
- Tech Scout
- Unparalleled Data Quality
- Higher Quality Content
- 60% Fewer Hallucinations
Browse by: Latest US Patents, China's latest patents, Technical Efficacy Thesaurus, Application Domain, Technology Topic, Popular Technical Reports.
© 2025 PatSnap. All rights reserved.Legal|Privacy policy|Modern Slavery Act Transparency Statement|Sitemap|About US| Contact US: help@patsnap.com