Preparation method of easy-to-wash active printing thickener
A reactive printing and paste technology, which is applied in the fields of dyeing, textiles and paper making, can solve the problems of composite printing paste printing effect and the inability to improve the depaste rate at the same time, and achieve low cost, easy depaste, and soft hand feeling Effect
- Summary
- Abstract
- Description
- Claims
- Application Information
AI Technical Summary
Problems solved by technology
Method used
Image
Examples
Embodiment 1
[0051] The easy-to-clean reactive printing paste of this embodiment was prepared with the raw material components described in Table 1. Wherein, the degree of substitution of sodium carboxymethyl cellulose is 1.0, and the degree of substitution of sodium carboxymethyl starch is 1.0.
[0052] The preparation method of the easy-washing active printing paste comprises the steps:
[0053] At room temperature, add sodium carboxymethyl cellulose, sodium carboxymethyl starch, lithium magnesium silicate, polyvinylpyrrolidone, and sodium lauryl sulfate into the conical mixer, start the agitator, and add the wetting component ( Isomerized tridecanyl alcohol polyoxyethylene ether and fatty alcohol polyoxyethylene ether sodium sulfate), the per minute feeding amount of the wetting component is 15% (the percentage is the weight percentage that the per minute feeding amount accounts for the wetting component total amount ), after stirring for 15 minutes, add sodium citrate, sodium gluconat...
Embodiment 2
[0055] The easy-to-clean reactive printing paste of this embodiment was prepared with the raw material components described in Table 1. Wherein, the degree of substitution of sodium carboxymethyl cellulose is 1.2, and the degree of substitution of sodium carboxymethyl starch is 1.0.
[0056] At room temperature, add sodium carboxymethyl cellulose, sodium carboxymethyl starch, lithium magnesium silicate, polyvinylpyrrolidone, and sodium lauryl sulfate into the conical mixer, start the agitator, and add the wetting component ( Isomerized tridecanyl alcohol polyoxyethylene ether and fatty alcohol polyoxyethylene ether sodium sulfate), the per minute feeding amount of the wetting component is 20% (the percentage is the weight percentage that the per minute feeding amount accounts for the wetting component total amount ), after stirring for 20 minutes, add sodium citrate, sodium gluconate, sodium chloride, sodium sulfate, and stir for 45 minutes.
Embodiment 3
[0058] The easy-to-clean reactive printing paste of this embodiment was prepared with the raw material components described in Table 1. Wherein, the degree of substitution of sodium carboxymethyl cellulose is 1.5, and the degree of substitution of sodium carboxymethyl starch is 1.2.
[0059] At room temperature, add sodium carboxymethyl cellulose, sodium carboxymethyl starch, lithium magnesium silicate, polyvinylpyrrolidone, and sodium lauryl sulfate into the conical mixer, start the agitator, and add the wetting component ( Isomerized tridecanyl alcohol polyoxyethylene ether and fatty alcohol polyoxyethylene ether sodium sulfate), the per minute feeding amount of the wetting component is 20% (the percentage is the weight percentage that the per minute feeding amount accounts for the wetting component total amount ), after stirring for 10 minutes, add sodium citrate, sodium gluconate, sodium chloride, sodium sulfate, and stir for 45 minutes.
PUM
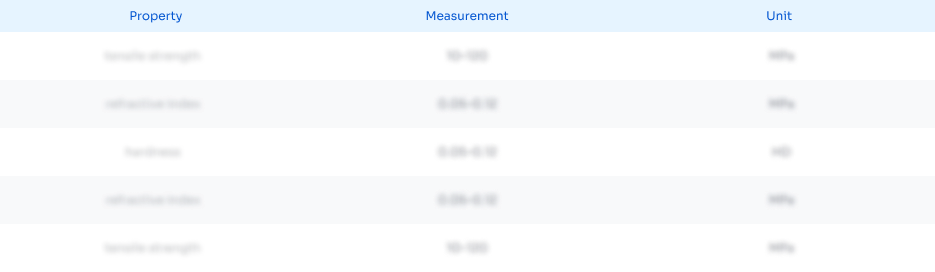
Abstract
Description
Claims
Application Information

- Generate Ideas
- Intellectual Property
- Life Sciences
- Materials
- Tech Scout
- Unparalleled Data Quality
- Higher Quality Content
- 60% Fewer Hallucinations
Browse by: Latest US Patents, China's latest patents, Technical Efficacy Thesaurus, Application Domain, Technology Topic, Popular Technical Reports.
© 2025 PatSnap. All rights reserved.Legal|Privacy policy|Modern Slavery Act Transparency Statement|Sitemap|About US| Contact US: help@patsnap.com