Method for preparing silicomanganese with high silicon
A high-silicon-silicon-manganese alloy and mixture technology, applied in the field of metal smelting, can solve the problems of difficult production, high production cost, and high raw material requirements, and achieve the effects of high grade rate, lower cost, and low power consumption
- Summary
- Abstract
- Description
- Claims
- Application Information
AI Technical Summary
Problems solved by technology
Method used
Image
Examples
Embodiment 1
[0042] In this embodiment, ferrosilicon is used as the silicon-containing raw material, and silicon-manganese water-quenched slag is used as the covering agent to detect the influence of the covering agent on the recovery rate of different elements in the alloy, the recovery rate of the alloy, and the smelting conditions.
[0043] 1. Experimental method:
[0044] The experimental group used silicomanganese water quenching slag as the covering agent, and the control group did not add covering agent, and carried out smelting. The specific method is as follows:
[0045] (1) 40Kg of silicomanganese (manganese 66.38%, silicon 16.41) is smelted by submerged arc furnace to obtain liquid silicomanganese alloy;
[0046](2) Utilize the intermediate frequency furnace to smelt 13Kg of ferrosilicon (0.4% manganese, 70% silicon), wherein, when the ferrosilicon turns red, the experimental group adds 5Kg of silicon-manganese water quenching slag for smelting to obtain liquid ferrosilicon allo...
Embodiment 2
[0051] In this embodiment, ferrosilicon is used as the silicon-containing raw material, silicon-manganese water-quenched slag and carbon-manganese dry slag are respectively used as covering agents, and the recovery rate of different elements in the alloy, the recovery rate of the alloy, and the change of phosphorus content are detected.
[0052] 1. Experimental method:
[0053] The first group uses silicon-manganese water-quenched slag as the covering agent, and the second group uses carbon-manganese dry slag as the covering agent for smelting. The specific methods are as follows:
[0054] (1) Utilize submerged arc furnace to smelt silicon-manganese and carbon-manganese, wherein, the addition of silicon-manganese and carbon-manganese is shown in Table 2, to obtain liquid silicon-manganese alloy;
[0055] (2) Utilize the industrial frequency furnace to smelt ferrosilicon, and add covering agent to smelt together when it turns red, wherein, the addition amount of ferrosilicon an...
Embodiment 3
[0061] In this embodiment, industrial silicon is used as the silicon-containing raw material to detect the recovery rate of silicon element in industrial silicon and the recovery rate of each element in the alloy;
[0062] 1. Experimental method:
[0063] (1) Utilize submerged arc furnace to smelt silicon-manganese and carbon-manganese, wherein, the addition of silicon-manganese and carbon-manganese is shown in Table 3, to obtain liquid silicon-manganese alloy;
[0064] (2) Utilize the industrial frequency furnace to smelt industrial silicon, and add silicomanganese water-quenched slag to smelt together when it turns red, wherein, the addition amount of industrial silicon and silicomanganese-manganese water-quenched slag is shown in Table 2 to obtain liquid ferrosilicon alloy;
[0065] (3) Add the liquid silicon manganese alloy into the industrial frequency furnace, mix it with the liquid silicon ferrosilicon alloy, and remelt it at 1650 degrees Celsius to obtain the high sili...
PUM
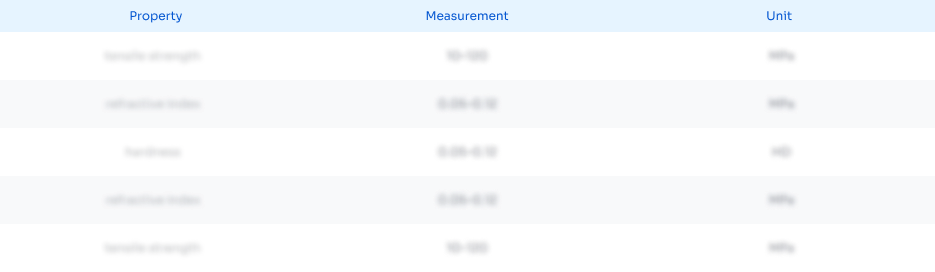
Abstract
Description
Claims
Application Information

- Generate Ideas
- Intellectual Property
- Life Sciences
- Materials
- Tech Scout
- Unparalleled Data Quality
- Higher Quality Content
- 60% Fewer Hallucinations
Browse by: Latest US Patents, China's latest patents, Technical Efficacy Thesaurus, Application Domain, Technology Topic, Popular Technical Reports.
© 2025 PatSnap. All rights reserved.Legal|Privacy policy|Modern Slavery Act Transparency Statement|Sitemap|About US| Contact US: help@patsnap.com