Polyamide-6 filament production technology
A production process and technology of nylon, which is applied in the field of nylon, can solve the problems of poor elasticity and poor comfort, and achieve the effect of improving performance, comfort and tightness
- Summary
- Abstract
- Description
- Claims
- Application Information
AI Technical Summary
Problems solved by technology
Method used
Examples
Embodiment 1
[0021] (1) Prepare raw materials, by weight, take by weight 60 parts of nylon 6, 4 parts of modified antibacterial and anti-ultraviolet functional masterbatches, 8 parts of sulfite, 8 parts of polycaprolactone, 7 parts of sodium fluoride, Among them, the modified antibacterial and anti-ultraviolet functional masterbatch, in parts by weight, includes 40 parts of nylon 6 slices, 0.3 parts of polycaprolactone, and 3 parts of zirconium sodium silver phosphate. , slice the raw materials separately;
[0022] (2) Use a nitrogen flow to continuously dry the slices of nylon 6, and the drying temperature is 160°C;
[0023] (3) Put the dried polyamide 6 slices, modified antibacterial and anti-ultraviolet functional masterbatch, antioxidant, dispersant, and catalyst into the screw extruder to melt, and the melt is transported to the metering pump for metering after passing through the static mixer , after being extruded by the spinning machine, it is cooled to form filaments, and the fil...
Embodiment 2
[0026] (1) Prepare raw materials, by weight, take by weight 65 parts of nylon 6, 5 parts of modified antibacterial and anti-ultraviolet functional masterbatches, 6 parts of sulfite, 5 parts of polycaprolactone, 8 parts of sodium silicate, Among them, the modified antibacterial and anti-ultraviolet functional masterbatch, in parts by weight, includes 35 parts of nylon 6 slices, 0.4 parts of polycaprolactone, and 5 parts of sodium zirconium phosphate. , slice the raw materials separately;
[0027] (2) Use a nitrogen flow to continuously dry the slices of nylon 6, and the drying temperature is 170°C;
[0028] (3) Put the dried polyamide 6 slices, modified antibacterial and anti-ultraviolet functional masterbatch, antioxidant, dispersant, and catalyst into the screw extruder to melt, and the melt is transported to the metering pump for metering after passing through the static mixer , after being extruded by a spinning machine, it is cooled to form filaments, and the filaments ar...
PUM
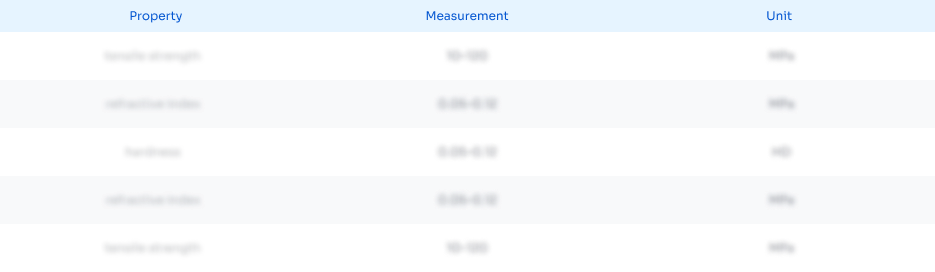
Abstract
Description
Claims
Application Information

- Generate Ideas
- Intellectual Property
- Life Sciences
- Materials
- Tech Scout
- Unparalleled Data Quality
- Higher Quality Content
- 60% Fewer Hallucinations
Browse by: Latest US Patents, China's latest patents, Technical Efficacy Thesaurus, Application Domain, Technology Topic, Popular Technical Reports.
© 2025 PatSnap. All rights reserved.Legal|Privacy policy|Modern Slavery Act Transparency Statement|Sitemap|About US| Contact US: help@patsnap.com