Hot drawing technology for 410# steel cylinders
A heat-drawing and steel cylinder technology, which is applied in the field of gas cylinder processing, can solve problems such as gas cylinder leakage, potential safety hazards, excessive wall thickness difference of containers, etc., and achieve the effect of avoiding shortened service life and improving rolling precision
- Summary
- Abstract
- Description
- Claims
- Application Information
AI Technical Summary
Problems solved by technology
Method used
Examples
Embodiment Construction
[0017] The present invention will be further described below through specific examples.
[0018] A 410 material steel cylinder hot drawing process is characterized in that it comprises the following steps:
[0019] Material selection: choose 410 stainless steel plate as the blank, calculate the size according to the size of the steel cylinder, and then use a cutting machine to cut the blank into circular plates according to the calculated target size;
[0020] Mold fixing: select the hot drawing mold according to the cut circular plate, the mold has at least three mold positions with successively deeper depths, fix the mold on the clamping machine, and clean the mold;
[0021] Annealing: Place the cut circular plate in an annealing furnace for annealing treatment. The annealing furnace maintains a temperature of 800~940°C for 15 minutes, and then cools rapidly;
[0022] Grinding: Grinding the surface to remove the burrs;
[0023] Deep drawing: place the polished blank at the...
PUM
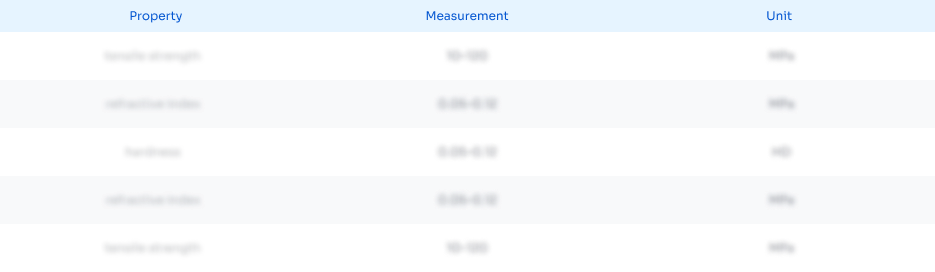
Abstract
Description
Claims
Application Information

- Generate Ideas
- Intellectual Property
- Life Sciences
- Materials
- Tech Scout
- Unparalleled Data Quality
- Higher Quality Content
- 60% Fewer Hallucinations
Browse by: Latest US Patents, China's latest patents, Technical Efficacy Thesaurus, Application Domain, Technology Topic, Popular Technical Reports.
© 2025 PatSnap. All rights reserved.Legal|Privacy policy|Modern Slavery Act Transparency Statement|Sitemap|About US| Contact US: help@patsnap.com