Robot tail end positioning deviation correction method and system
A correction method and a correction system technology, applied to instruments, measuring devices, optical devices, etc., can solve problems such as the influence of galvanometer correction and the large error in position deviation calculation
- Summary
- Abstract
- Description
- Claims
- Application Information
AI Technical Summary
Problems solved by technology
Method used
Image
Examples
Embodiment Construction
[0031] figure 1 Shown is a schematic structural diagram of a general robot end positioning deviation correction system of the present invention. The general robot end correction system refers to correcting the spatial positioning error of the manipulator end to obtain a spatial position error correction table. The invention mainly uses industrial cameras and visual algorithms to obtain the positioning deviation of the robot end, obtains the error distribution of the robot's positioning, and software compensation makes the robot's end positioning more accurate.
[0032] In order to realize the high-precision end positioning of the robot, the present invention proposes a universal robot end calibration system, which includes: a manipulator 10, an execution end 11 located at the end of the manipulator 10, an object calibration plate 20 for the execution end 11 to work, and a fixed and driven The high-precision motion platform 30 on which the calibration plate 20 moves, and the im...
PUM
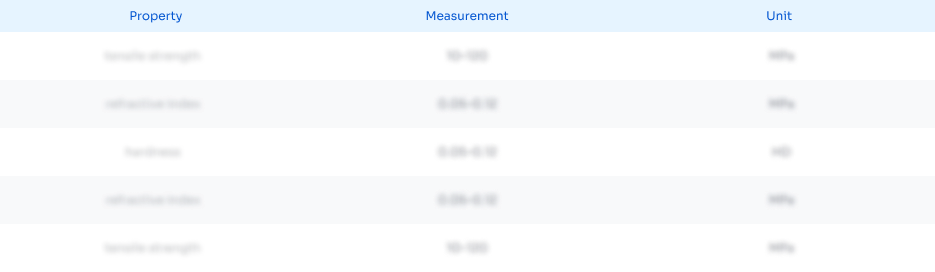
Abstract
Description
Claims
Application Information

- R&D
- Intellectual Property
- Life Sciences
- Materials
- Tech Scout
- Unparalleled Data Quality
- Higher Quality Content
- 60% Fewer Hallucinations
Browse by: Latest US Patents, China's latest patents, Technical Efficacy Thesaurus, Application Domain, Technology Topic, Popular Technical Reports.
© 2025 PatSnap. All rights reserved.Legal|Privacy policy|Modern Slavery Act Transparency Statement|Sitemap|About US| Contact US: help@patsnap.com