Digital printing circular-screen sizing machine
A digital printing and rotary screen technology, applied in textiles and papermaking, liquid/gas/steam textile material processing, textile material processing, etc., can solve the problems of increasing washing time, wasting pulp, wasting water resources, etc., and achieve improvement Production efficiency, full automation, uniform sizing effect
- Summary
- Abstract
- Description
- Claims
- Application Information
AI Technical Summary
Problems solved by technology
Method used
Image
Examples
Embodiment Construction
[0017] Such as figure 1 As shown, the digital printing rotary screen sizing machine includes an organic table 1 and a conveying device 2, an edge blowing device 3, a circulation device 4, a cleaning device 5, a tensioning device 6 and a driving device 7 arranged on the machine table 1. The driving device 7 is drivingly connected to the conveying device 2, the edge blowing device 3 and the circulating device 4; the conveying device 2 includes a cloth guide roller 21; the edge blowing device 3 includes an edge blowing device 31, a thread separating roller 32, a cloth pressing roller 33 and a pressure bearing The roller 34, the cloth guide roller 21, the edge blower 31, the thread separating roller 32, and the cloth pressing roller 33 are sequentially connected from right to left and arranged above the machine table 1; the circulation device 4 is arranged on the upper part of the machine table 1, and the circulation device 4 includes There are an endless conveyor belt 41, an activ...
PUM
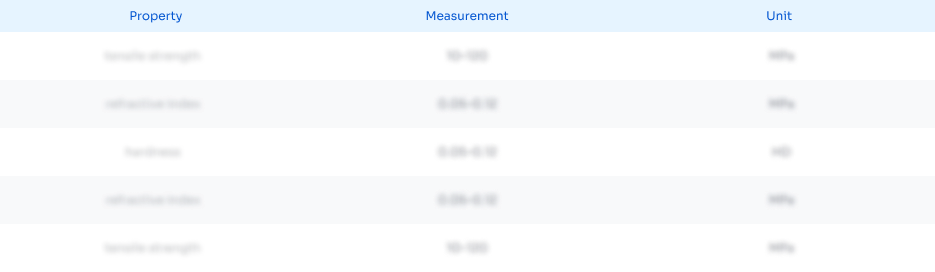
Abstract
Description
Claims
Application Information

- R&D Engineer
- R&D Manager
- IP Professional
- Industry Leading Data Capabilities
- Powerful AI technology
- Patent DNA Extraction
Browse by: Latest US Patents, China's latest patents, Technical Efficacy Thesaurus, Application Domain, Technology Topic, Popular Technical Reports.
© 2024 PatSnap. All rights reserved.Legal|Privacy policy|Modern Slavery Act Transparency Statement|Sitemap|About US| Contact US: help@patsnap.com