Wet method electrolytic metal full-automatic production system
A technology for electrolysis of metals and production systems, applied in the direction of instrument, optics, process efficiency improvement, etc., can solve problems such as unfavorable energy saving and environmental protection, inconvenient production operation, failure to realize automation, etc., achieve a high degree of production intensification, and reduce direct production. cost, the effect of reducing production operators
- Summary
- Abstract
- Description
- Claims
- Application Information
AI Technical Summary
Problems solved by technology
Method used
Image
Examples
Embodiment 1
[0033] Such as figure 1 , figure 2 , image 3 As shown, a fully automated production system for wet electrolytic metal mainly includes a large unit tank 6, a cathode strip 2, a cathode strip transmission mechanism, a sliding conductive device, a load-bearing guide rail device, and an anode conductive device. The cathode strip 2 It is set as a closed ring belt, and a sealing device 4 is arranged on the outside of the large cell 6, and the cathode plate belt 2 is provided with retaining cylinders 3 near the two sides of the large cell 6, which are used to adjust the cathode plate belt 2 in the cathode chamber. s position.
[0034] The cathode strip transmission mechanism is mainly composed of a transmission drum 1, a retaining cylinder 3, and an electric mechanism 20. As an optimal solution, it is equipped with a synchronous motor and an intelligent controller to keep the cathode strip 2 moving smoothly and evenly. The unit has a large groove A plurality of driving rollers 1...
Embodiment 2
[0045] A fully automatic production system for wet electrolytic metal in this implementation is basically the same structure as in Example 1, the difference is that in the production process of electrolytic manganese, after the cathode strip 2 passes through the large cell 6, it is sequentially Enter passivation device 15, cleaning product device 14, drying device 13, stripping device 11, plate washing device 10, polishing device 9, dipping glass water device 8, starting electrolytic cell 7, and then return to the large cell 6 of the unit.
[0046] The passivation device 15 is mainly composed of two rollers with sponges and a device for spraying passivation solution. The rollers are respectively attached to the two sides of the cathode strip 2, and the passivation solution is injected into the sponge from time to time. 2, the passivation solution is evenly coated on the metal manganese to complete the passivation.
[0047] The cleaning product device 14 is mainly composed of a...
PUM
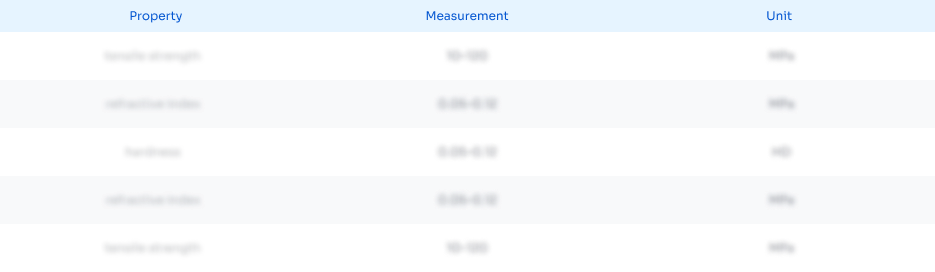
Abstract
Description
Claims
Application Information

- R&D Engineer
- R&D Manager
- IP Professional
- Industry Leading Data Capabilities
- Powerful AI technology
- Patent DNA Extraction
Browse by: Latest US Patents, China's latest patents, Technical Efficacy Thesaurus, Application Domain, Technology Topic, Popular Technical Reports.
© 2024 PatSnap. All rights reserved.Legal|Privacy policy|Modern Slavery Act Transparency Statement|Sitemap|About US| Contact US: help@patsnap.com