High-aluminum low-silicon casting material
A castable, low-silicon technology, applied in the field of refractory materials, can solve the problems of low compressive strength, achieve the effects of enhanced erosion resistance, improved thermal shock resistance, and reduced CaO content
- Summary
- Abstract
- Description
- Claims
- Application Information
AI Technical Summary
Problems solved by technology
Method used
Image
Examples
Embodiment 1
[0018] A high-alumina and low-silicon castable, the components and the mass percentages of the components are as follows: low-silicon dense fused white corundum 3-5mm accounts for 20%, low-silicon dense fused white corundum 1-3mm accounts for 20%, and low-silicon dense fused white corundum 1-3mm accounts for 20%. Silicon dense fused white corundum 0~1mm accounts for 20%, alumina micropowder α-A accounts for 1%, activated alumina ρ-A accounts for 2%, nano-sized ZrO 2 3%, alumina and zirconia 1%, CA-70 pure calcium aluminate cement 8%, 320 mesh fused white corundum 25%. Low-silicon dense fused white corundum 1-3 mm means that the particle size of low-silicon dense fused white corundum is within the range of 1-3 mm.
[0019] The properties and comparative values of the high-aluminum-low-silicon castable prepared in this example are as follows:
[0020] One: The compressive strength at high temperature is improved, as shown in the following table:
[0021] temperature...
Embodiment 2
[0025] A high-alumina and low-silicon castable, the components and the mass percentages of the components are as follows: low-silicon dense fused white corundum 3-5mm accounts for 23%, low-silicon dense fused white corundum 1-3mm accounts for 22%, and low-silicon dense fused white corundum 1-3mm accounts for 22%. Silicon dense fused white corundum 0~1mm accounts for 15%, alumina micropowder α-A accounts for 3%, activated alumina ρ-A accounts for 4%, nano-sized ZrO 2 4%, alumina and zirconia 3%, CA-70 pure calcium aluminate cement 6%, 320 mesh fused white corundum 20%.
[0026] The properties and comparative values of the high-aluminum-low-silicon castable prepared in this example are as follows:
[0027] One: The compressive strength at high temperature is improved, as shown in the following table:
[0028] temperature value
conventional material
this invention
at 1095°C
54.6MPa
85MPa
at 1370°C
67.8 MPa
92MPa
[0029] ...
Embodiment 3
[0032] A high-alumina and low-silicon castable, the components and the mass percentages of the components are as follows: low-silicon dense fused white corundum 3-5mm accounts for 30%, low-silicon dense fused white corundum 1-3mm accounts for 16%, and low-silicon dense fused white corundum 1-3mm accounts for 16%. Silicon dense fused white corundum 0~1mm accounts for 11%, alumina micropowder α-A accounts for 5%, activated alumina ρ-A accounts for 7%, nano-sized ZrO 2 6%, alumina and zirconia 5%, CA-70 pure calcium aluminate cement 3%, 320 mesh fused white corundum 17%.
[0033] The properties and comparative values of the high-aluminum-low-silicon castable prepared in this example are as follows:
[0034] One: The compressive strength at high temperature is improved, as shown in the following table:
[0035] temperature value
conventional material
this invention
at 1095°C
54.6MPa
83 MPa
[0036] at 1370°C
67.8 MPa
90M...
PUM
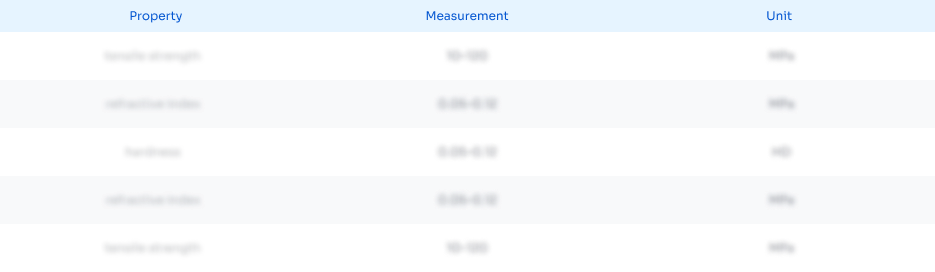
Abstract
Description
Claims
Application Information

- Generate Ideas
- Intellectual Property
- Life Sciences
- Materials
- Tech Scout
- Unparalleled Data Quality
- Higher Quality Content
- 60% Fewer Hallucinations
Browse by: Latest US Patents, China's latest patents, Technical Efficacy Thesaurus, Application Domain, Technology Topic, Popular Technical Reports.
© 2025 PatSnap. All rights reserved.Legal|Privacy policy|Modern Slavery Act Transparency Statement|Sitemap|About US| Contact US: help@patsnap.com