Forming process for net corrugated board structure of cloth dyeing machine
A molding process and cloth dyeing machine technology, applied in the field of bending, can solve the problems of plate bending part springback, plate breakage, etc., and achieve the effects of less surface scratches, stable products, and good batch reproducibility
- Summary
- Abstract
- Description
- Claims
- Application Information
AI Technical Summary
Problems solved by technology
Method used
Image
Examples
Embodiment 1
[0031] Fabric dyeing machine net corrugated plate structure forming process, the process includes the following steps:
[0032] Step 1: Cut the board into flat boards according to the calculated expanded size of the corrugated board;
[0033] Step 2: The plate is polished and affixed with a protective film;
[0034] Step 3: Place the flat plate on the workbench of the bending machine, and carry out the bending process on the flat plate through the bending machine and the bending die.
[0035] Press and fold to form a plurality of arc-shaped convex lines 1 in the middle of the flat plate;
[0036] Step 4: Bending both sides of the plate inwards with a bending machine and a folding die;
[0037] Step 5: Oil treatment on the surface of the plate.
[0038] The crimping mold in step 3 is a corrugated plate mold. The bending machine performs one-time crimping of the flat plate through the corrugated plate mold. The corrugated plate mold includes a corrugated plate mold and a corr...
Embodiment 2
[0040] Same as Example 1, the difference is that the creasing mold in Example 1 is changed into a wave-shaped mold and a tooth-shaped mold. Both the wave-shaped mold and the tooth-shaped mold have a matching base. The mold and the tooth-shaped mold are pressed and formed. First, the wave-shaped mold is used to corrugate the flat plate to form a wave plate, and then the wave valley of the wave plate is folded twice through the tooth-shaped mold. Eleven rectangular teeth 6 are arranged on the working surface of the tooth-shaped mold, and the distance between the rectangular teeth 6 is the same as that of the wave valleys of the wave-shaped mold. The valley becomes a horizontal plane, thus forming a corrugated board structure with convex columns on the surface. Before proceeding to step 2, the plates were heat treated. Both the pressure-pressurizing spiral tube 7 is installed on the creasing mold and the flanging mold, and the side of the creasing mold and the side of the flangi...
PUM
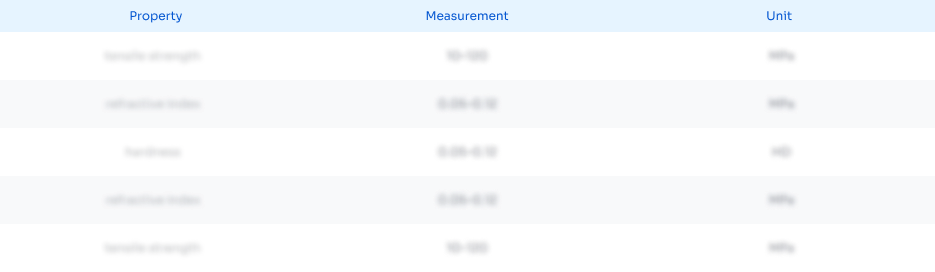
Abstract
Description
Claims
Application Information

- Generate Ideas
- Intellectual Property
- Life Sciences
- Materials
- Tech Scout
- Unparalleled Data Quality
- Higher Quality Content
- 60% Fewer Hallucinations
Browse by: Latest US Patents, China's latest patents, Technical Efficacy Thesaurus, Application Domain, Technology Topic, Popular Technical Reports.
© 2025 PatSnap. All rights reserved.Legal|Privacy policy|Modern Slavery Act Transparency Statement|Sitemap|About US| Contact US: help@patsnap.com