Cross resistance welding process for heterogeneous wires
A criss-cross and resistance welding technology, applied in resistance welding equipment, manufacturing tools, welding equipment, etc., can solve the problems of increased contact area, large cold deformation of wire, and reduced heat production, so as to reduce contact resistance and increase Strength, the effect of a good connection
- Summary
- Abstract
- Description
- Claims
- Application Information
AI Technical Summary
Problems solved by technology
Method used
Image
Examples
Embodiment Construction
[0018] The present invention works and implements in this way, a cross resistance welding process of dissimilar wires, which is characterized in that the process steps are as follows: a multi-pulse DC resistance welding machine is used, and the welding wires are placed between two electrodes perpendicular to each other. , the upper electrode 1 moves down to clamp the welded wire, and the current is applied after contact, the double pulse current waveform is selected, and the electrode pressure is adjusted in coordination. After the welding cycle is completed, the upper electrode 1 and the lower electrode 2 are automatically separated, and different wires are crossed. Resistance welded joints.
[0019] In cardiac pacemakers, stainless steel pins are welded to platinum-iridium alloy electrode wires using this method. Before welding, the material to be welded is ultrasonically cleaned in acetone, then rinsed with alcohol and dried. The resistance welding system used is composed ...
PUM
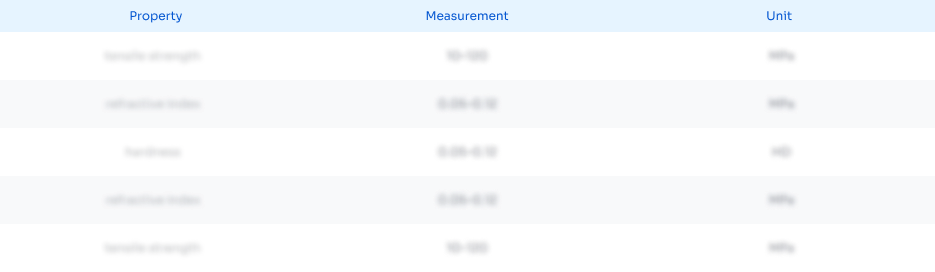
Abstract
Description
Claims
Application Information

- R&D
- Intellectual Property
- Life Sciences
- Materials
- Tech Scout
- Unparalleled Data Quality
- Higher Quality Content
- 60% Fewer Hallucinations
Browse by: Latest US Patents, China's latest patents, Technical Efficacy Thesaurus, Application Domain, Technology Topic, Popular Technical Reports.
© 2025 PatSnap. All rights reserved.Legal|Privacy policy|Modern Slavery Act Transparency Statement|Sitemap|About US| Contact US: help@patsnap.com