Method and structure for cooling flame tube of combustor
A technology of cooling structure and flame tube, which is applied in combustion methods, combustion chambers, continuous combustion chambers, etc., can solve the problems of difficulty in research and development, difficulty in meeting use requirements, etc., and achieve a good cooling effect.
- Summary
- Abstract
- Description
- Claims
- Application Information
AI Technical Summary
Problems solved by technology
Method used
Image
Examples
Embodiment Construction
[0026] The present invention will be further described below in conjunction with accompanying drawing:
[0027] Such as figure 1 As shown, a method for cooling the flame tube of the combustion chamber is to add a radiator 2 in the low-temperature environment outside the flame tube 1. When the flame tube 1 is working, the coolant is between the cavity 3 inside the wall of the flame tube 1 and the radiator 2 The heat of the wall of the flame tube 1 is transferred to the external low-temperature environment to protect the flame tube 1 from being burned out.
[0028] The present invention uses coolant and heat exchanger to cool the flame cylinder 1, without using compressor outlet air for cooling or using expensive new materials, and using existing superalloys to meet working conditions.
[0029] When the flame tube 1 is working, the low-temperature coolant flows into the cavity 3 of the wall of the flame tube 1, and convective heat exchange occurs with the wall of the flame tube...
PUM
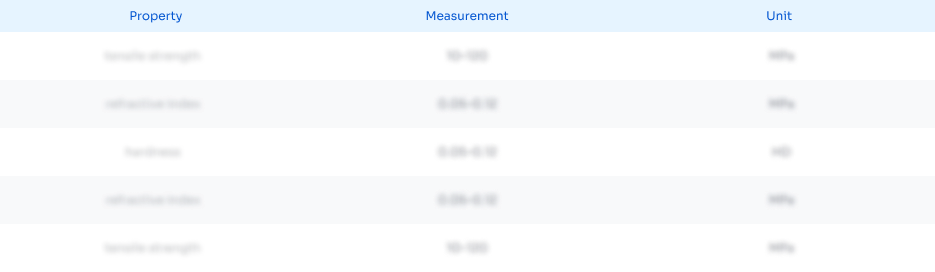
Abstract
Description
Claims
Application Information

- R&D Engineer
- R&D Manager
- IP Professional
- Industry Leading Data Capabilities
- Powerful AI technology
- Patent DNA Extraction
Browse by: Latest US Patents, China's latest patents, Technical Efficacy Thesaurus, Application Domain, Technology Topic, Popular Technical Reports.
© 2024 PatSnap. All rights reserved.Legal|Privacy policy|Modern Slavery Act Transparency Statement|Sitemap|About US| Contact US: help@patsnap.com