Self-centering micro drill bit without chisel edge
A self-centering, no chisel edge technology, used in repairing drills, drilling tool accessories, drilling/drilling equipment, etc., can solve problems such as reduced positioning accuracy, low service life, rough hole walls, etc., to improve the hole position. Accuracy and hole type accuracy, reduce wear and breakage, improve the effect of stress conditions
- Summary
- Abstract
- Description
- Claims
- Application Information
AI Technical Summary
Problems solved by technology
Method used
Image
Examples
Embodiment Construction
[0019] The present invention will be further described in detail below in conjunction with the accompanying drawings and embodiments.
[0020] This embodiment provides a self-centering micro-drill without a chisel edge, and the diameter range of the micro-drill that can be processed is tiny holes in between. See attached figure 1 , 2 , the chisel-free self-centering micro-drill has a two-stage drill point structure, including: drill body 7, a primary drill point and a secondary drill point; wherein the primary drill point starts from the drill body 7, and the secondary drill point starts from The top of the first-level drill point, and the apex of the second-level drill point is the drill core point 1. The drill body 7, the primary drill point and the secondary drill point are all located on the same axis.
[0021] The primary drill tip includes: two outer edges 5 and two outer edge flanks 6; the secondary drill tip includes: drill core tip 1, two inner edges 2, two inner...
PUM
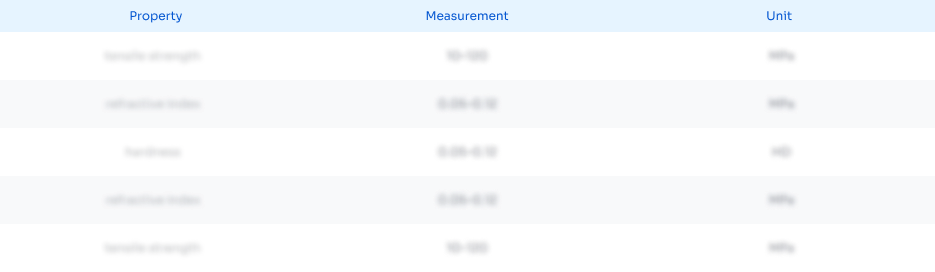
Abstract
Description
Claims
Application Information

- Generate Ideas
- Intellectual Property
- Life Sciences
- Materials
- Tech Scout
- Unparalleled Data Quality
- Higher Quality Content
- 60% Fewer Hallucinations
Browse by: Latest US Patents, China's latest patents, Technical Efficacy Thesaurus, Application Domain, Technology Topic, Popular Technical Reports.
© 2025 PatSnap. All rights reserved.Legal|Privacy policy|Modern Slavery Act Transparency Statement|Sitemap|About US| Contact US: help@patsnap.com