Method for synchronously machining flange plates at two ends of rear axle housing welding assembly
A technology of synchronous processing and rear axle housing, which is applied in the direction of metal processing equipment, metal processing machinery parts, manufacturing tools, etc., can solve the problem of inability to realize multi-variety, small and medium-sized batch production, work in turn, and cannot guarantee the coaxiality of the inner hole of the flange In order to achieve the effect of reducing processing costs, reducing floor space, and improving flexibility and adaptability
- Summary
- Abstract
- Description
- Claims
- Application Information
AI Technical Summary
Problems solved by technology
Method used
Image
Examples
Embodiment Construction
[0025] The invention provides a method for synchronously processing the flanges at both ends of the rear axle housing welding assembly, synchronously processing the outer circle, inner hole and end face of the flanges at both ends of the axle, and realizing multi-process processing in one clamping, avoiding the use of The clamping error caused by the processing of multiple machine tools can improve the machining accuracy, ensure the coaxiality of the outer circle and the inner hole, the coaxiality of the outer circle and the end face, and the coaxiality between the flanges at both ends, and reduce the machine tool. The floor area and processing time are reduced, the processing cost is reduced, and the processing quality and processing efficiency are improved.
[0026] Such as figure 2 As shown, the specific process steps for synchronously processing the flanges at both ends of the rear axle housing welding assembly are:
[0027] 1) Workpiece positioning and clamping: such as...
PUM
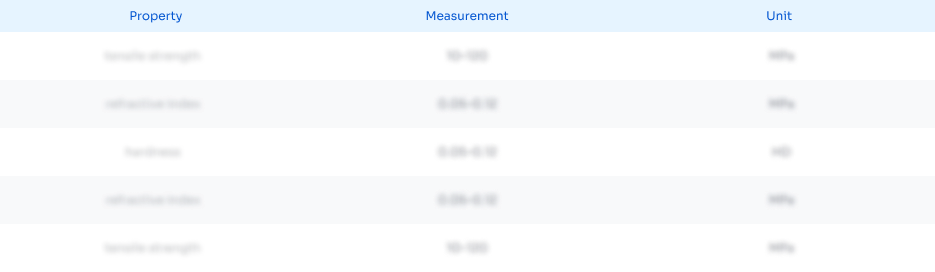
Abstract
Description
Claims
Application Information

- Generate Ideas
- Intellectual Property
- Life Sciences
- Materials
- Tech Scout
- Unparalleled Data Quality
- Higher Quality Content
- 60% Fewer Hallucinations
Browse by: Latest US Patents, China's latest patents, Technical Efficacy Thesaurus, Application Domain, Technology Topic, Popular Technical Reports.
© 2025 PatSnap. All rights reserved.Legal|Privacy policy|Modern Slavery Act Transparency Statement|Sitemap|About US| Contact US: help@patsnap.com