Method for imparting permanent long-lasting water repellency to textile structure
A fiber structure and fiber technology, which is applied in the field of waterproof fiber structure manufacturing, can solve the problems that the waterproof performance cannot reach the fiber dyeing process, etc., and achieve the effects of improving oil resistance, excellent friction resistance/wear resistance, and preventing dust adhesion Effect
- Summary
- Abstract
- Description
- Claims
- Application Information
AI Technical Summary
Problems solved by technology
Method used
Image
Examples
Embodiment 1
[0139] First, the cotton 100% padding No. 30 warp and weft interwoven fabric (woven into a width of 152cm, length of 50m, weight 34.56kg), using indanthrene dye (also called reduction dyeing dye = vat dye): continuous Press dyeing-drying-reduction steaming, soaping-drying step operation, you can get dyed finished products. Use it to prepare 300m (total weight 207.36kg). Afterwards, the dyed product is given a fiber modifier by the bath immersion method. Then dry it, and use a fluorine-based waterproofing agent to perform: press dyeing-drying-heat treatment to obtain a waterproof cotton fabric. The operation will be described in more detail below.
[0140] (1) Pre-treatment of fiber modifier
[0141] Weigh out a 10% by mass aqueous solution of the pure component of the reaction mixture of 2,6-dichloro-4-hydroxy-1,3,5-triazine sodium salt and diaminobenzenesulfonate sodium salt, so that the weight of the fiber is 16 %Owm (33.18kg) amount. Afterwards, it was put into a circular d...
Embodiment 2
[0159] First, 100% woolen No. 52 / 1 line 2 / 2 No. 2 serge is dyed with 1:2 gold-containing dye. The dyed cloth is pre-treated with a fiber modifier by the bath immersion method. Secondly, water-proof woolen serge can be obtained by waterproofing. Hereinafter, the operation will be described in more detail.
[0160] (1) Pre-treatment of fiber modifier
[0161] First put in the winch: 20% owm fiber modifier pure component 10% by mass solution, 2g / L 48% acetic acid aqueous solution. Next, put the dyed woolen serge into the winch. Then adjust the pH of the solution in the winch to 5.2. The treatment bath volume, 1ton bath ratio is 1:30.
[0162] After that, the operation starts from the bath temperature of 30°C, and the temperature is raised at a rate of 1°C / min. After it reaches 60°C, the operation is performed at a constant temperature for 15 minutes. After that, the temperature was raised again at a rate of 2°C / min, and after it reached 80°C, it was operated for another 30 minutes...
Embodiment 3
[0174] First prepare 400m (total weight 148kg) 100% nylon 6 cloth 110t-20f Oxford cloth 148cm×50m=18.5kg, and then use jet dyeing machine 2200L (liquor ratio 1:15) for dyeing, washing and fixing Treatment (using phenolic synthetic fixing agent). After that, it was operated with a fiber modifier by a bath immersion method, and then a fluorine-based water repellent was used to obtain a water-repellent nylon 6. Hereinafter, the operation will be described in more detail.
[0175] (1) Pre-treatment of fiber modifier
[0176] First, a bath solution prepared with a 20% owm (29.6 kg) fiber modifier with a purity of 15% and a 0.25 g / L malic acid was put into the dyeing machine. Then put the dyed nylon 6 into it, and then start the operation at the bath temperature of 30°C. After that, the temperature is increased at a cloth speed of 380m / min and 2°C / min. After it reaches 60°C, it is operated at a constant temperature for 15 minutes. After that, the temperature was increased at a rate o...
PUM
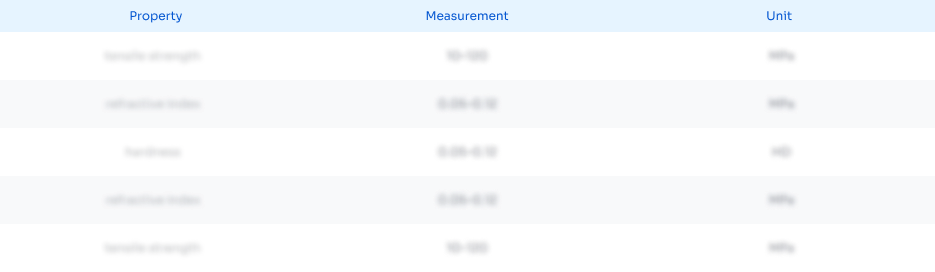
Abstract
Description
Claims
Application Information

- R&D
- Intellectual Property
- Life Sciences
- Materials
- Tech Scout
- Unparalleled Data Quality
- Higher Quality Content
- 60% Fewer Hallucinations
Browse by: Latest US Patents, China's latest patents, Technical Efficacy Thesaurus, Application Domain, Technology Topic, Popular Technical Reports.
© 2025 PatSnap. All rights reserved.Legal|Privacy policy|Modern Slavery Act Transparency Statement|Sitemap|About US| Contact US: help@patsnap.com