Chromium salt mud treatment method
A treatment method, chromium salt technology, applied in chemical instruments and methods, chromium compounds, inorganic chemistry, etc., can solve problems such as easy production of other impurities, difficult trivalent chromium, leaching, etc.
- Summary
- Abstract
- Description
- Claims
- Application Information
AI Technical Summary
Problems solved by technology
Method used
Image
Examples
Embodiment approach
[0093] A processing method for chromium salt mud, comprising the following steps:
[0094] (1) Mix chromium salt mud and water at a mass volume ratio (g / mL) of 1:(2-20) and heat to 30-100°C for elution for 0.2-4 hours. After liquid-solid separation, the surface-adsorbed chromium and soluble Salt filtrate and filter residue, the filtrate is returned to the chlorate production system for recycling;
[0095] (2) Mix the filter residue obtained in step (1) with water at a mass volume ratio (g / mL) of 1:(2-20) and mix evenly, with the molar ratio of oxidant and chromium in the filter residue being (5-50):1 Add the oxidizing agent in an amount of leaching agent, mix and heat to 30-200°C for 0.5-4h to oxidize, add the leaching agent with the molar ratio of leaching agent to calcium element in the filter residue (0.5-5):1, mix and heat at 30-200°C Leach for 0.5 to 6 hours, and obtain the leach liquid and leach residue after liquid-solid separation;
[0096] (3) The leached slag obtai...
Embodiment 1
[0100] (1) Mix 40g of chromium salt mud and water at a mass volume ratio (g / mL) of 1:2 and heat to 100°C for elution for 0.2h. After liquid-solid separation, the filtrate and filter residue containing chromium adsorbed on the surface and soluble salts are obtained. The filtrate is returned to the chlorate production system for recycling;
[0101] (2) Mix the filter residue obtained in step (1) with water at a mass volume ratio (g / mL) of 1:20, add hydrogen peroxide at a molar ratio of 5:1 to the chromium element in the filter residue, mix and heat to 30 Oxidation at ℃ for 4 hours, adding potassium carbonate in the amount of potassium carbonate and calcium element in the filter residue at a molar ratio of 5:1, mixing and heating at 200℃ for 0.5h, and obtaining the leaching solution and leaching residue after liquid-solid separation;
[0102] (3) The leaching slag obtained in step (2) is washed in 5 stages to obtain dechrome tailings, the liquid-solid ratio (mL / g) of washing is 2...
Embodiment 2
[0107] (1) Mix 40g of chromium salt mud and water at a mass volume ratio (g / mL) of 1:20 and heat to 30°C for elution for 4 hours. After liquid-solid separation, the filtrate and filter residue containing chromium adsorbed on the surface and soluble salts are obtained. Return to the chlorate production system for recycling;
[0108] (2) Mix the filter residue obtained in step (1) with water at a mass volume ratio (g / mL) of 1:2, add hydrogen peroxide in an amount of 5:1 molar ratio of the chromium element in the hydrogen peroxide to the filter residue, mix and heat to 200 Oxidation at 0.5°C for 0.5h, adding sodium carbonate at a molar ratio of 0.5:1 to the calcium element in the filter residue, mixing and heating at 30°C for 6h, and obtaining the leach solution and leach residue after liquid-solid separation;
[0109] (3) The leached slag obtained in step (2) is subjected to two-stage washing to obtain dechrome tailings, the liquid-solid ratio (mL / g) of the washing is 8:1, the w...
PUM
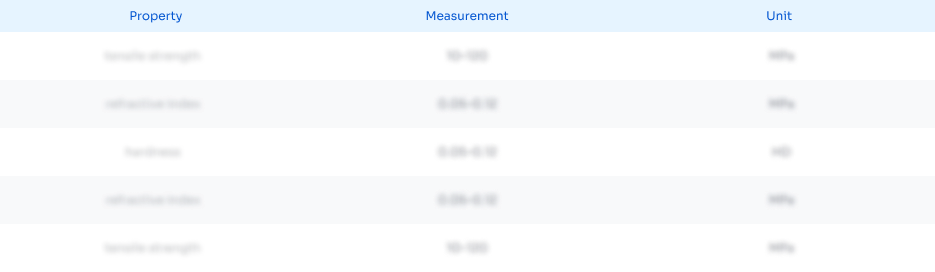
Abstract
Description
Claims
Application Information

- R&D Engineer
- R&D Manager
- IP Professional
- Industry Leading Data Capabilities
- Powerful AI technology
- Patent DNA Extraction
Browse by: Latest US Patents, China's latest patents, Technical Efficacy Thesaurus, Application Domain, Technology Topic, Popular Technical Reports.
© 2024 PatSnap. All rights reserved.Legal|Privacy policy|Modern Slavery Act Transparency Statement|Sitemap|About US| Contact US: help@patsnap.com