Underwater friction stitch welding local dry method small draining device
A technology of local dry method and drainage device, applied in welding equipment, non-electric welding equipment, metal processing equipment, etc., can solve problems such as poor welding quality
- Summary
- Abstract
- Description
- Claims
- Application Information
AI Technical Summary
Problems solved by technology
Method used
Image
Examples
Embodiment Construction
[0013] The technical solutions of the present invention will be further described below in conjunction with specific embodiments.
[0014] as attached figure 1 and 2 As shown, the structure of the drainage device of the present invention, wherein 1 is a drainage cover, 2 is an observation window, 3 is a drainage sponge layer, 4 is an air inlet hole, 5 is a sealing material layer, 6 is a stopper rod, and 7 is a workpiece to be welded .
[0015] The entire drainage cover is a cylindrical shell with an opening at the lower end, and a plane is milled symmetrically in the vertical direction to facilitate the installation of the observation window; a through hole is set at the center of the upper end surface of the drainage cover, and a sealing material layer is set in the through hole; The air intake holes are arranged symmetrically on the left and right sides of the through hole to facilitate the connection of the air pipe for ventilation, so as to ensure the air environment in ...
PUM
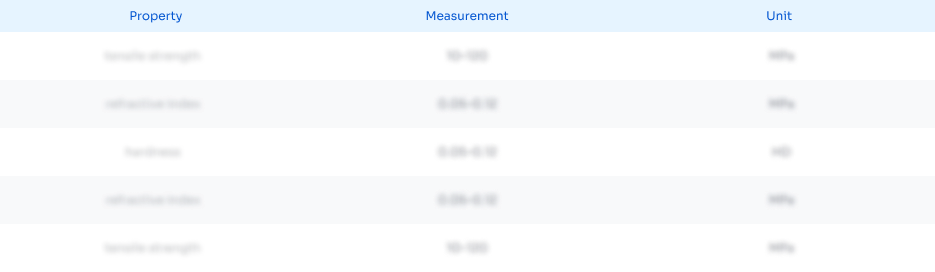
Abstract
Description
Claims
Application Information

- Generate Ideas
- Intellectual Property
- Life Sciences
- Materials
- Tech Scout
- Unparalleled Data Quality
- Higher Quality Content
- 60% Fewer Hallucinations
Browse by: Latest US Patents, China's latest patents, Technical Efficacy Thesaurus, Application Domain, Technology Topic, Popular Technical Reports.
© 2025 PatSnap. All rights reserved.Legal|Privacy policy|Modern Slavery Act Transparency Statement|Sitemap|About US| Contact US: help@patsnap.com