A rotary tunnel kiln
A tunnel kiln and rotary technology, applied in the kiln field, can solve the problems of cost increase, resource consumption, and easy production of defective products, and achieve the effects of uniform temperature distribution, reduced heating frequency, and improved product quality
- Summary
- Abstract
- Description
- Claims
- Application Information
AI Technical Summary
Problems solved by technology
Method used
Image
Examples
Embodiment 1
[0021] refer to figure 1 , figure 2 , image 3 and Figure 4 , a rotary tunnel kiln, comprising an annular kiln body 1 composed of an inner wall 111 and an outer wall 112 and a track arranged at the inner bottom of the kiln body 1, one end of the kiln body 1 is a feed inlet 113, and the other end is an outlet Material opening 114, the inside of the kiln body 1 is a drying chamber 11, a primary oxidation chamber 12, a secondary oxidation chamber 13, a firing chamber 14 and a cooling chamber 15 in sequence from the feed inlet 113 to the discharge outlet 114. The two side walls of each kiln chamber in the kiln body 1 except the cooling chamber 15 are provided with six spiral iron-chromium-aluminum heating wires 2 of the same specification from top to bottom, and the power of the heating wires in the drying chamber 11 is 42kw , the power of the heating wire in the primary oxidation chamber 12 is 60kw, the power of the heating wire in the secondary oxidation chamber 13 is 80kw,...
Embodiment 2
[0023] refer to Figure 5 , a rotary tunnel kiln, comprising an annular kiln body 1 composed of an inner wall 111 and an outer wall 112 and a track arranged at the inner bottom of the kiln body 1, one end of the kiln body 1 is a feed inlet 113, and the other end is an outlet Material port 114, the inside of the kiln body 1 is a drying chamber 11, a primary oxidation chamber 12, a secondary oxygen chamber 13, a firing chamber 14 and a cooling chamber 15 in sequence from the feed port 113 to the discharge port 114. The two side walls of each kiln chamber except the cooling chamber 15 in the kiln body 1 are provided with six helical iron-chromium-aluminum heating wires 2 of the same specification from top to bottom, and the heating wires on the side walls of the firing chamber are connected to the The length ratio of the heating wires on the inner wall is 0.9:1. The spiral iron-chromium-aluminum heating wires 2 in each kiln chamber are connected to the same circuit and controlled...
PUM
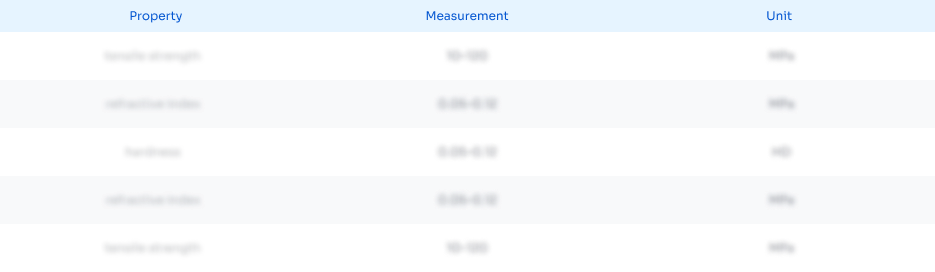
Abstract
Description
Claims
Application Information

- R&D Engineer
- R&D Manager
- IP Professional
- Industry Leading Data Capabilities
- Powerful AI technology
- Patent DNA Extraction
Browse by: Latest US Patents, China's latest patents, Technical Efficacy Thesaurus, Application Domain, Technology Topic, Popular Technical Reports.
© 2024 PatSnap. All rights reserved.Legal|Privacy policy|Modern Slavery Act Transparency Statement|Sitemap|About US| Contact US: help@patsnap.com