Oxidative absorption system and method for producing acrylic acid from propylene
A technology of producing acrylic acid from propylene and oxidative absorption, which is applied in chemical instruments and methods, organic chemistry, carboxylate preparation, etc. It can solve the problems of high risk, tray flooding, large desalinated water, etc., and reduce equipment occupation The effect of reducing the floor area, reducing the number of equipment, and reducing the number of connecting pipes
- Summary
- Abstract
- Description
- Claims
- Application Information
AI Technical Summary
Problems solved by technology
Method used
Image
Examples
specific Embodiment 1
[0039] An oxidative absorption system for propylene to acrylic acid, such as figure 1 As shown, it includes a propylene vaporization tower 1, a first oxidation reactor 2, a second oxidation reactor 3 and a three-in-one tower 4. The top of the propylene vaporization tower 1 is provided with a mixing superheater 5, and the top outlet of the mixing superheater 5 is connected to the The top inlet of the first oxidation reactor 2 is connected, the bottom outlet of the first oxidation reactor 2 is connected with the top inlet of the second oxidation reactor 3, the bottom outlet of the second oxidation reactor 3 is connected with the lower end inlet of the three-in-one tower 4 Connection, the connecting pipeline between the mixing superheater 5 and the first oxidation reactor 2 is provided with a first feed mixer 6, and the connecting pipeline between the first oxidation reactor 2 and the second oxidation reactor 3 is provided with a second feed A mixer 7, a product steam generator 8...
specific Embodiment 2
[0043] A method for preparing acrylic acid by utilizing the above-mentioned specific embodiment—an oxidation absorption system for producing acrylic acid from propylene, specifically comprising the following steps:
[0044] 1) Send liquid propylene into propylene vaporization tower 1 to be vaporized into propylene gas and refined, then mix propylene gas with 1.6MPAG steam and send it to mixing superheater 5, mix propylene steam with water vapor and superheat to 50-70℃ ; Wherein the molar ratio of water vapor to propylene is (1.5-1.8): 1;
[0045] 2) After the fresh air is compressed by the air compressor 15, and the exhaust gas from the three-in-one tower 4 after catalytic incineration is boosted by the exhaust gas compressor 16 (the return amount is 25-40 wt of the total incineration exhaust gas %), and the mixed gas of propylene and water vapor from the mixing superheater 5 is sent to the first feed mixer 6 for mixing, and then sent to the upper reaction zone of the first ox...
specific Embodiment 3
[0049] The liquid propylene with a propylene content of 99%wt and an oligomer and heavy component content of 0.5%wt is sent to the propylene vaporization tower 1 for propylene gasification and refining, and the 2.0 MPAG steam from the oxidation reactor by-product is sent to the propylene vaporization tower 1 The top of the mixture is mixed with vaporized propylene and enters the mixing superheater 5 at the top of the propylene vaporization tower 1. By controlling the flow of heating steam, the temperature of the material at the outlet of the mixing superheater 5 is controlled to be 60°C.
[0050] The composition of tail gas after incineration is: nitrogen: 77.4%wt, water: 13.7%wt, carbon dioxide: 6.5%, oxygen: 2.4%.
[0051] The amount of fresh air fed into the first feed mixer 6 is controlled to ensure that propylene: oxygen: water (molar ratio) = 1:1.7:1 in the mixture at the outlet of the first feed mixer 6 . The mixed gas meeting the composition requirements is sent to the...
PUM
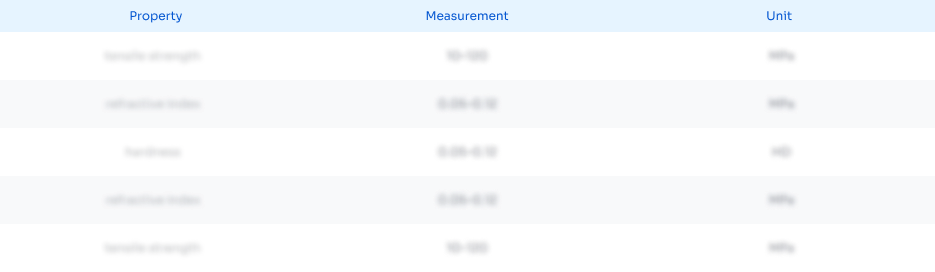
Abstract
Description
Claims
Application Information

- R&D Engineer
- R&D Manager
- IP Professional
- Industry Leading Data Capabilities
- Powerful AI technology
- Patent DNA Extraction
Browse by: Latest US Patents, China's latest patents, Technical Efficacy Thesaurus, Application Domain, Technology Topic, Popular Technical Reports.
© 2024 PatSnap. All rights reserved.Legal|Privacy policy|Modern Slavery Act Transparency Statement|Sitemap|About US| Contact US: help@patsnap.com