Inspection and evaluation system for track geometric irregularity
A technology for evaluating systems and tracks, applied in railway vehicle shape measuring instruments, railway car body parts, railway auxiliary equipment, etc. The effect of improving efficiency and improving detection accuracy
- Summary
- Abstract
- Description
- Claims
- Application Information
AI Technical Summary
Problems solved by technology
Method used
Image
Examples
specific Embodiment approach 1
[0024] Specific implementation mode one: combine figure 1 , figure 2 , image 3 , Figure 4 , Figure 5 with Image 6 Describe this embodiment, this embodiment comprises the locomotive 1 that moves independently on the track to be tested, the excitation system 2 that is arranged in locomotive 1, control system 3, signal acquisition system 4, navigation system 5 and signal processing system 6;
[0025] The vibration excitation system 2 is used to apply continuous vibration excitation to the running locomotive 1, and transmit the vibration excitation to the track to be detected through the locomotive 1;
[0026] The control system 3 is used to control the coordinated work of the entire detection system. By controlling the running speed of the locomotive 1, the excitation frequency and the excitation amplitude of the vibration excitation system 2, the wheel rails of the locomotive 1 and the track to be detected are stay in contact at all times;
[0027] The signal acquisit...
specific Embodiment approach 2
[0033] Specific implementation mode two: combination figure 1 , figure 2 , image 3 , Figure 4 with Figure 5 This embodiment is described. In this embodiment, the locomotive 1 runs at a predetermined speed on the track to be tested or the locomotive 1 is driven by a tractor. The wheel-rail distance of the locomotive 1 can be adjusted according to the type of track to be tested. Other structures and connections are the same as those in the first embodiment.
specific Embodiment approach 3
[0034] Specific implementation mode three: combination figure 1 with figure 2 This embodiment is described. In this embodiment, the vibration excitation system 2 is arranged on the chassis of the locomotive 1 and is located on the central axis of the chassis. The excitation end of the vibration excitation system 2 is connected to the chassis of the locomotive 1 . Other structures and connections are the same as those in the second embodiment.
PUM
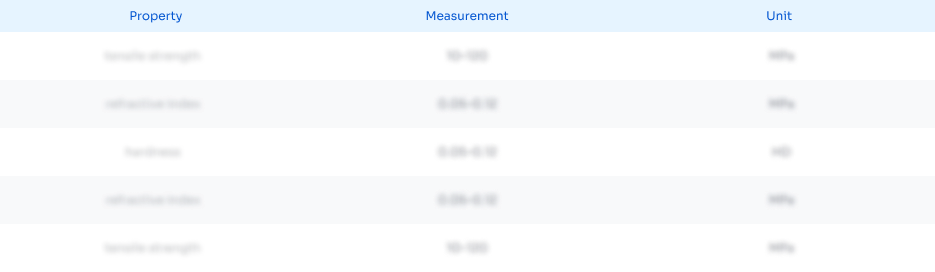
Abstract
Description
Claims
Application Information

- R&D
- Intellectual Property
- Life Sciences
- Materials
- Tech Scout
- Unparalleled Data Quality
- Higher Quality Content
- 60% Fewer Hallucinations
Browse by: Latest US Patents, China's latest patents, Technical Efficacy Thesaurus, Application Domain, Technology Topic, Popular Technical Reports.
© 2025 PatSnap. All rights reserved.Legal|Privacy policy|Modern Slavery Act Transparency Statement|Sitemap|About US| Contact US: help@patsnap.com