Mixed sintering ore
A technology of mixing sintering and sintering ore, applied in the furnace, blast furnace details, blast furnace and other directions, can solve the problems of rising, unfavorable to improve furnace conditions and blast furnace technical indicators, and the proportion of sintering ore cannot be further improved, so as to reduce consumption, The effect of improving blast furnace conditions and reducing emissions
- Summary
- Abstract
- Description
- Claims
- Application Information
AI Technical Summary
Problems solved by technology
Method used
Examples
Embodiment Construction
[0010] The present invention will be further described in detail below in conjunction with specific embodiments.
[0011] The mixed sintered ore is formed by mixing acidic sintered ore with a basicity of 0.6-0.8 and basic sintered ore with a basicity of 1.8-2.3 in a weight ratio of 1:3-5. In this embodiment, the basicity of the acidic sintered ore is 0.7, the basicity of the basic sintered ore is 1.85, and the weight ratio of the acidic sintered ore and the basic sintered ore in the mixed sintered ore is 1:4; and the acidic sintered ore The weight content of each component is as follows: SiO 2 : 5.80~6.20%, CaO: 3.80~4.60%, MgO: 0.80~1.20%, Al 2 o 3 : 1.30~1.90%, FeO: 8~12%, TFe: 55~61%. In addition, the particle size of 5-35mm in the acid sinter is greater than 70%, and the drum strength of the acid sinter: 65-70%. The weight content, particle size and drum strength of each component of the acid sinter are set in such a way that the acid sinter can be better used for blas...
PUM
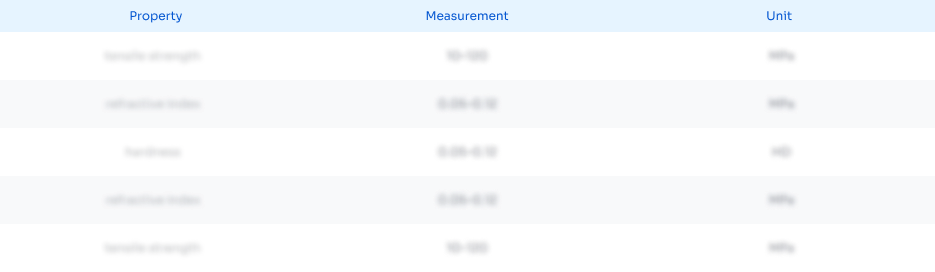
Abstract
Description
Claims
Application Information

- R&D
- Intellectual Property
- Life Sciences
- Materials
- Tech Scout
- Unparalleled Data Quality
- Higher Quality Content
- 60% Fewer Hallucinations
Browse by: Latest US Patents, China's latest patents, Technical Efficacy Thesaurus, Application Domain, Technology Topic, Popular Technical Reports.
© 2025 PatSnap. All rights reserved.Legal|Privacy policy|Modern Slavery Act Transparency Statement|Sitemap|About US| Contact US: help@patsnap.com