Manufacturing technology and equipment of shoe outsole
A manufacturing process and shoe outsole technology, which is applied in the field of shoe outsole manufacturing process and equipment, can solve the problems of uneven spray dyeing, easy spraying to other parts of the shoe outsole, difficult vulcanization of rubber and polyurethane, etc., to achieve Shape-rich effects
- Summary
- Abstract
- Description
- Claims
- Application Information
AI Technical Summary
Problems solved by technology
Method used
Image
Examples
Embodiment Construction
[0012] The technology will be further described below.
[0013] The manufacturing process of present embodiment shoe outsole is as Figure 5 : a. produce the rubber base 7 of the flat shoe outsole, b. prepare the upper mold and the lower mold of the shoe outsole, c. prepare a PU film 3, and the PU film 3 can be made into a formulated color during production, Also can spray required pattern on PU film 3 after making, because PU film 3 is planar, so can greatly improve the quality of spray pattern, coat adhesive on rubber substrate 7 or PU film 3 , d. Place the rubber base 7 at the bottom of the lower mold, such as Figure 5 In step 1., e. spread PU film 3 on lower mold 2, as Figure 5 In step ②, if the PU film 3 has a pattern, the side with the pattern is facing down, f. adopt a plastic-absorbing process, use a pressure ring 4 to press the surroundings of the PU film 3, and then start the exhaust fan 6 from the bottom The bottom of the mold is ventilated, because in order to...
PUM
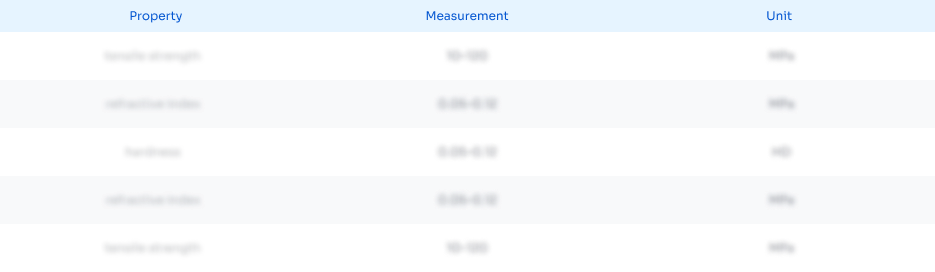
Abstract
Description
Claims
Application Information

- R&D Engineer
- R&D Manager
- IP Professional
- Industry Leading Data Capabilities
- Powerful AI technology
- Patent DNA Extraction
Browse by: Latest US Patents, China's latest patents, Technical Efficacy Thesaurus, Application Domain, Technology Topic, Popular Technical Reports.
© 2024 PatSnap. All rights reserved.Legal|Privacy policy|Modern Slavery Act Transparency Statement|Sitemap|About US| Contact US: help@patsnap.com