Method for producing wood pulp sponge
A production method and technology of sponge products, applied in the direction of coating, etc., can solve the problems of easy deterioration, hardening, non-degradable regeneration, environmental pollution, etc.
- Summary
- Abstract
- Description
- Claims
- Application Information
AI Technical Summary
Problems solved by technology
Method used
Examples
Embodiment 1
[0041] A method for making wood pulp sponge, which uses wood pulp as the main raw material, and after soaking, pressing, yellowing, viscose, mixing, foaming and washing processes, it is made into a degradable wood cellulose sponge product , each procedure in the described preparation method is:
[0042] a) Soaking process, add 20% sodium hydroxide and wood pulp into the soaking tank and mix together to make wood pulp liquid, wherein the weight ratio of sodium hydroxide and wood pulp is 2:1;
[0043] The immersion temperature in the immersion barrel is 30°C, and under the condition of high-speed rotation, the immersion barrel is carried out under two working conditions: intermittent and continuous;
[0044] b) Squeezing process, put the soaked wood pulp into the press, squeeze out too much sodium hydroxide solution to obtain the compressed alkali cellulose block, and then put the alkali cellulose block for 1.5 hours carry out aging treatment;
[0045] The dryness of the compr...
Embodiment 2
[0055] A production method of wood pulp sponge, which selects wood pulp as the main raw material, and makes degradable wood cellulose sponge products after soaking, pressing, yellowing, viscose, mixing, foaming and washing. , the various procedures in the manufacturing method are:
[0056] a) In the soaking process, sodium hydroxide with a concentration of 12% and wood pulp are added to the soaking barrel and mixed together to make wood pulp, wherein the weight ratio of sodium hydroxide and wood pulp is 1.5:1;
[0057] The dipping temperature in the dipping bucket is 25°C, and under the condition of high-speed rotation, the dipping bucket is carried out in two working states: intermittent and continuous;
[0058] b) Pressing process, put the soaked wood pulp into the press, squeeze out the excess sodium hydroxide solution to obtain the compressed alkali cellulose block, and then let the alkali cellulose block stand for 1 hour aging treatment;
[0059] The dryness of the comp...
Embodiment 3
[0070] A production method of wood pulp sponge, which selects wood pulp as the main raw material, and makes degradable wood cellulose sponge products after soaking, pressing, yellowing, viscose, mixing, foaming and washing. , it is characterized in that each process in the described production method is:
[0071] a) soaking process, adding sodium hydroxide with a concentration of 28% and wood pulp in the soaking barrel to mix together to make wood pulp, wherein the weight ratio of sodium hydroxide and wood pulp is 2.5:1;
[0072] The dipping temperature in the dipping barrel is 35°C, and under the condition of high-speed rotation, the dipping barrel is carried out in two working states: intermittent and continuous;
[0073] b) Pressing process, put the soaked wood pulp into the press, squeeze out the excess sodium hydroxide solution to obtain the compressed alkali cellulose block, and then let the alkali cellulose block stand for 2 hours aging treatment;
[0074] The dryness...
PUM
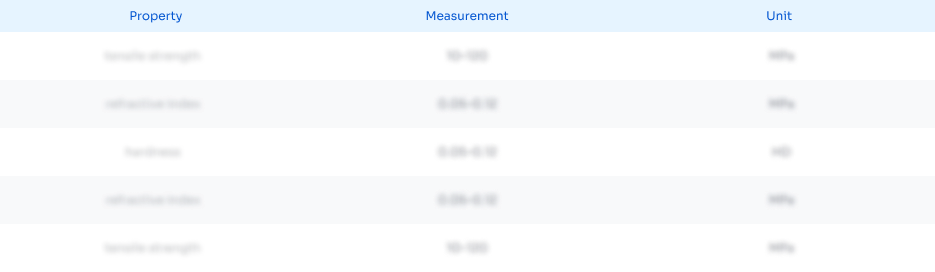
Abstract
Description
Claims
Application Information

- Generate Ideas
- Intellectual Property
- Life Sciences
- Materials
- Tech Scout
- Unparalleled Data Quality
- Higher Quality Content
- 60% Fewer Hallucinations
Browse by: Latest US Patents, China's latest patents, Technical Efficacy Thesaurus, Application Domain, Technology Topic, Popular Technical Reports.
© 2025 PatSnap. All rights reserved.Legal|Privacy policy|Modern Slavery Act Transparency Statement|Sitemap|About US| Contact US: help@patsnap.com