High-precision temporary punching type injecting transonic speed wind tunnel flow field control structure
A control structure and ejection technology, applied in the direction of electric fluid pressure control, etc., can solve the problem that the control quantity cannot directly act on the controlled quantity, the effect of the total pressure of the main exhaust valve lags behind, and the Mach number cannot be directly measured, etc. problem, achieve the effects of suppressing model attitude disturbance, improving control performance, and reducing data measurement waiting time
- Summary
- Abstract
- Description
- Claims
- Application Information
AI Technical Summary
Problems solved by technology
Method used
Image
Examples
Embodiment Construction
[0042] The present invention takes the domestic 2.4m temporary ejection type transonic wind tunnel as an example to illustrate the implementation of the invented control structure and method.
[0043] The structure of the flow field control system of the 2.4m temporary ejection type transonic wind tunnel is as follows: figure 1As shown, the generalized wind tunnel object is in the dotted box. In order to eliminate the influence of the reduction of the air source pressure on the flow field of the wind tunnel during the wind tunnel test, the main pilot pressure control loop is introduced, and the control of the wind tunnel flow field is decomposed into two parts: the main pilot pressure control and the total pressure static pressure control, as shown in figure 2 shown. The control structure is composed of three modules: the set value calculation model, the main pilot controller, and the flow field controller. In the main pilot pressure control part, the main pressure regulati...
PUM
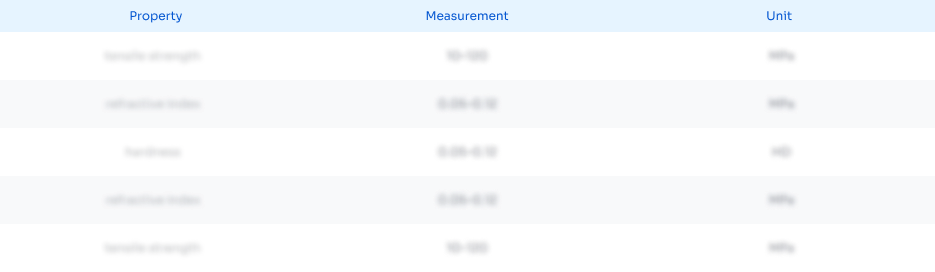
Abstract
Description
Claims
Application Information

- R&D
- Intellectual Property
- Life Sciences
- Materials
- Tech Scout
- Unparalleled Data Quality
- Higher Quality Content
- 60% Fewer Hallucinations
Browse by: Latest US Patents, China's latest patents, Technical Efficacy Thesaurus, Application Domain, Technology Topic, Popular Technical Reports.
© 2025 PatSnap. All rights reserved.Legal|Privacy policy|Modern Slavery Act Transparency Statement|Sitemap|About US| Contact US: help@patsnap.com