Method for recovering exhaust gas according to polyolefin gas phase method
A recovery method and technology for polyolefins, applied in separation methods, chemical instruments and methods, nitrogen purification/separation, etc., can solve the problems of low recovery efficiency, unfriendly environment, large consumption of raw materials, etc., to reduce material consumption and flare emissions The effect of high volume, high recovery rate and low energy consumption
- Summary
- Abstract
- Description
- Claims
- Application Information
AI Technical Summary
Problems solved by technology
Method used
Image
Examples
Embodiment 1
[0049] Such as figure 1 As shown, the polypropylene homopolymer is produced by the gas phase fluidized bed process, the reaction temperature is 66° C., and the reaction pressure is 3.38 MPag. Driven by the conveying carrier gas, the solid polypropylene discharged from the reactor enters the vertical product receiver through the discharge system, and the residual hydrocarbons in the polypropylene are removed by nitrogen purge, and the exhaust gas 1 is firstly recovered after being filtered The air cooler B1 is cooled to 42°C, and then enters the compression and condensation process. The outlet pressure of the first compressor B2 is 0.28MPag, and the outlet temperature of the first cooler B3 is 42°C; the outlet pressure of the second compressor B4 is 1.14MPag, and the outlet pressure of the second compressor B4 is 1.14MPag. The outlet temperature of the second cooler B5 is 42°C; the outlet pressure of the third compressor B6 is 4.10MPag, and the outlet temperature of the third c...
Embodiment 2
[0055] Such as figure 2 As shown, the ethylene-butene copolymerized linear low density polyethylene LLDPE is produced by the gas phase fluidized bed process, the reaction temperature is 88°C, the reaction pressure is 2.1MPag, and the condensation operation is adopted, and the condensing agent is isopentane. The solid polyethylene discharged from the reactor is driven by the carrier gas, and enters the degassing chamber through the discharge system, and the residual unreacted monomer and solvent in the polyethylene are removed by nitrogen purge, and the exhaust gas 1 is filtered and firstly After being cooled to 42°C by the recovery gas cooler B1, it enters the multi-stage compression and condensation process. The outlet pressure of the compressor is 2.0MPag, and the outlet temperature of the cooler is 20°C. The compressed, condensed and separated uncondensed gas 2 enters the heat exchanger B8 to be cryogenically cooled and then enters the gas-liquid separator B9 for separatio...
PUM
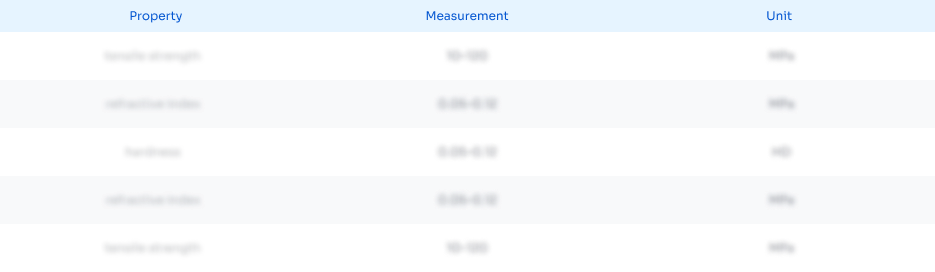
Abstract
Description
Claims
Application Information

- R&D
- Intellectual Property
- Life Sciences
- Materials
- Tech Scout
- Unparalleled Data Quality
- Higher Quality Content
- 60% Fewer Hallucinations
Browse by: Latest US Patents, China's latest patents, Technical Efficacy Thesaurus, Application Domain, Technology Topic, Popular Technical Reports.
© 2025 PatSnap. All rights reserved.Legal|Privacy policy|Modern Slavery Act Transparency Statement|Sitemap|About US| Contact US: help@patsnap.com