Radial guide blade structure with streamline structure
A technology of radial guide vanes and guide vanes, which is applied to components of pumping devices for elastic fluids, mechanical equipment, non-variable pumps, etc. Problems such as too large placement angle, to achieve the effect of not easy to vortex, smooth flow path, and reduce circulation
- Summary
- Abstract
- Description
- Claims
- Application Information
AI Technical Summary
Problems solved by technology
Method used
Image
Examples
Embodiment Construction
[0019] For ease of understanding, combined here Figure 2-4 Concrete structure of the present invention and implementation effect are further described as follows:
[0020] The specific structure of the present invention is as Figure 2-4 As shown, it is located in the annular space of the radial guide vane, at the position A where the tip of the positive guide vane 10 is located, that is, at the transition section, and the guide surface d for arc transition is set to make the fluid change direction smoothly. The arc where the diversion surface d is located changes according to the law that the radius of curvature gradually decreases from the starting point to the end point of the arc, and the arc can be simplified into two or more arcs at the same time. And as figure 2 and Figure 4 As shown, the anti-guide vane 20 adopts the method of conformal transformation and is designed according to the streamline. The curvature radius of the blade bone line gradually decreases from...
PUM
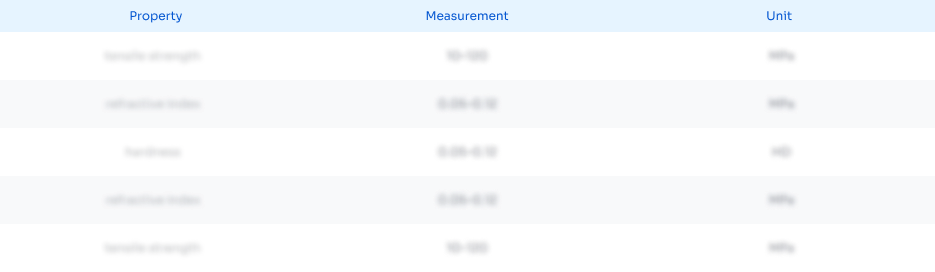
Abstract
Description
Claims
Application Information

- R&D
- Intellectual Property
- Life Sciences
- Materials
- Tech Scout
- Unparalleled Data Quality
- Higher Quality Content
- 60% Fewer Hallucinations
Browse by: Latest US Patents, China's latest patents, Technical Efficacy Thesaurus, Application Domain, Technology Topic, Popular Technical Reports.
© 2025 PatSnap. All rights reserved.Legal|Privacy policy|Modern Slavery Act Transparency Statement|Sitemap|About US| Contact US: help@patsnap.com