A device and process for producing methane by utilizing high-concentration CO
A high-concentration methane production technology, which is applied in high-concentration CO methane production equipment and methane production equipment field, can solve the problems of difficult catalyst process, inability to ensure outlet gas, high temperature rise, etc., and achieve controllable High performance, reduced external water supply, and reduced recycling costs
- Summary
- Abstract
- Description
- Claims
- Application Information
AI Technical Summary
Problems solved by technology
Method used
Image
Examples
Embodiment 1
[0025] according to Figure 1 The process conditions, the split ratio of imported raw material gas is 1:1, the ratio of circulating gas volume is 0.6, the volume of imported gas and water vapor is 0.8:1, and the changes of process parameters of each stage of logistics are shown in Table 1.
[0026] Table 1 Process parameters of each section of logistics
[0027]
[0028]In Example 1, it can be seen from simulation calculations that when the inlet feed gas split ratio is 1:1, the recycle gas volume is 0.6, and the inlet gas volume and water vapor volume are 0.8:1, the outlet temperature of the three-stage reactor does not exceed 500°C, and the product The methane content in the gas is >26%, which meets the process design requirements.
Embodiment 2
[0030] according to Figure 1 The process conditions, the split ratio of imported raw material gas is 0.6:1, the ratio of circulating gas volume is 0.5, the volume of imported gas and water vapor is 0.8:1, and the changes of process parameters of each stage of logistics are shown in Table 2.
[0031] Table 2 Process parameters of each section of logistics
[0032]
[0033] In Example 2, it can be seen through simulation calculation that when the split ratio of imported raw material gas is 0.6:1, the volume of circulating gas is 0.5, and the volume of imported gas and water vapor is 0.8:1, the outlet temperature of the three-stage reactor does not exceed 500 °C, and the product The methane content in the gas is >26%, which meets the process design requirements.
Embodiment 3
[0035] according to Figure 1 The process conditions, the split ratio of imported raw material gas is 1:1, the ratio of circulating gas volume is 0.7, the volume of imported gas and water vapor is 0.8:1, and the changes of process parameters of each stage of logistics are shown in Table 3.
[0036] Table 3 Process parameters of each section of logistics
[0037]
[0038] In Example 3, it can be seen through simulation calculation that when the split ratio of the imported raw material gas is 1:1, the circulating gas volume is 0.7, and the volume of the imported gas and water vapor is 0.8:1, the outlet temperature of the three-stage reactor does not exceed 500°C, and the product The methane content in the gas is >26%, which meets the process design requirements.
PUM
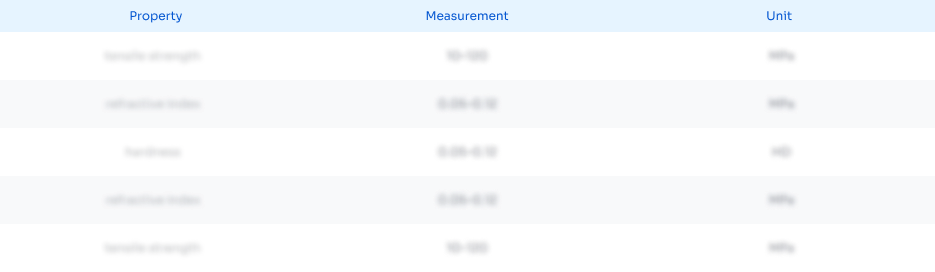
Abstract
Description
Claims
Application Information

- Generate Ideas
- Intellectual Property
- Life Sciences
- Materials
- Tech Scout
- Unparalleled Data Quality
- Higher Quality Content
- 60% Fewer Hallucinations
Browse by: Latest US Patents, China's latest patents, Technical Efficacy Thesaurus, Application Domain, Technology Topic, Popular Technical Reports.
© 2025 PatSnap. All rights reserved.Legal|Privacy policy|Modern Slavery Act Transparency Statement|Sitemap|About US| Contact US: help@patsnap.com