Fiber-enhanced cement-based composite material
A fiber-reinforced cement and composite material technology, applied in sustainable waste treatment, solid waste management, climate sustainability, etc., can solve the problems of high brittleness, inconvenient construction and maintenance, and achieve the effect of high interfacial bond strength
- Summary
- Abstract
- Description
- Claims
- Application Information
AI Technical Summary
Problems solved by technology
Method used
Examples
Embodiment 1
[0037] Cement 127 parts
[0038] 165 parts fine aggregate
[0039] Coarse aggregate 274 parts
[0040] Steel fiber 13 parts
[0041] Silica fume 21 parts
[0042] 14 parts volcanic ash
[0043] 23 parts of fly ash
[0044] Carbon nanotubes 18 parts
[0045] Inorganic lithium silicate binder 24 parts
[0046] 36 parts of water
[0047] 7 parts of water reducer
[0048] First add coarse aggregate and fiber into the mixer and stir for 1 minute, then add cement, fine aggregate, silica fume, volcanic ash, fly ash, and carbon nanotubes into the mixer in turn, continue stirring for 30 seconds, then mix water and water reducer, add Mixer, after stirring for 30s, add inorganic lithium silicate binder, continue stirring for 1min, and discharge the material to make test samples.
Embodiment 2
[0050] 147 parts of cement
[0051] 155 parts fine aggregate
[0052] Coarse aggregate 254 parts
[0053] Steel fiber 7 parts
[0054] High-strength and high-modulus polyethylene fiber 3 parts
[0055] Silica fume 22 parts
[0056] 12 parts volcanic ash
[0057] Fly ash 20 parts
[0058] Carbon nanotubes 16 parts
[0059] Inorganic lithium silicate binder 26 parts
[0060] 40 parts of water
[0061] 11 parts of water reducer
[0062] First add coarse aggregate and fiber into the mixer and stir for 1 minute, then add cement, fine aggregate, silica fume, volcanic ash, fly ash, and carbon nanotubes into the mixer in turn, continue stirring for 30 seconds, then mix water and water reducer, add Mixer, after stirring for 30s, add inorganic lithium silicate binder, continue stirring for 1min, and discharge the material to make test samples.
Embodiment 3
[0064] 157 parts of cement
[0065] 155 parts fine aggregate
[0066] Coarse aggregate 270 parts
[0067] Steel fiber 7 parts
[0068] High-strength and high-modulus micro-reinforced fiber 4 parts
[0069] Basalt fiber 2 parts
[0070] Silica fume 28 parts
[0071] 15 parts volcanic ash
[0072] Fly ash 19 parts
[0073] Carbon nanotubes 20 parts
[0074] Inorganic lithium silicate binder 25 parts
[0075] 43 parts of water
[0076] 6 parts of water reducer
[0077] First add coarse aggregate and fiber into the mixer and stir for 1 minute, then add cement, fine aggregate, silica fume, volcanic ash, fly ash, and carbon nanotubes into the mixer in sequence, continue stirring for 30 seconds, then mix water and water reducer, add Mixer, after stirring for 30s, add inorganic lithium silicate binder, continue stirring for 1min, and discharge the material to make test samples.
PUM
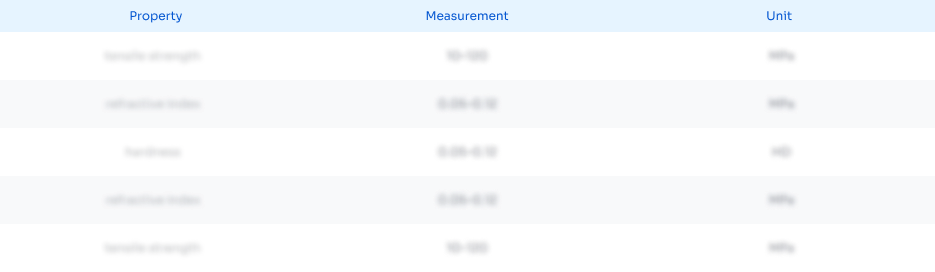
Abstract
Description
Claims
Application Information

- R&D Engineer
- R&D Manager
- IP Professional
- Industry Leading Data Capabilities
- Powerful AI technology
- Patent DNA Extraction
Browse by: Latest US Patents, China's latest patents, Technical Efficacy Thesaurus, Application Domain, Technology Topic, Popular Technical Reports.
© 2024 PatSnap. All rights reserved.Legal|Privacy policy|Modern Slavery Act Transparency Statement|Sitemap|About US| Contact US: help@patsnap.com