A natural environmental-friendly plant fiber board and a preparing method thereof
A plant fiber, natural and environmentally friendly technology, applied in the field of fiber board, can solve the problems of polluting the environment, fiber board is not environmentally friendly, etc., achieve low water absorption expansion rate, improve flexural strength and impact strength, high flexural strength and impact resistance sexual effect
- Summary
- Abstract
- Description
- Claims
- Application Information
AI Technical Summary
Problems solved by technology
Method used
Examples
Embodiment 1
[0056] Step 1: Take 15 parts of gum arabic, 7 parts of konjac gum, 12 parts of tapioca starch, 3 parts of calcium chloride, 10 parts of glycerin, and 46 parts of deionized water by weight, heat and stir until uniform;
[0057] Step 2: After the mixture in step 1 is evenly stirred, add 25 parts of lignocellulose, 11 parts of poplar fiber, 13 parts of eucalyptus fiber, 11 parts of sisal fiber, 4 parts of asparagus fiber, 6 parts of peanut fiber, 5 parts of pineapple leaf fiber, and then stir, and stir evenly;
[0058] Step 3: The material mixed in step 2 is subjected to high-temperature hot-press molding in a mold. The hot-pressing temperature is 120°C, and the hot-pressing pressure is 16MPa. After hot-pressing, it is cooled, and after cooling, it is cut into plates to obtain natural and environmentally friendly plant fibers. sheet.
Embodiment 2
[0060] Step 1: Take 10 parts of gum arabic, 4 parts of konjac gum, 25 parts of tapioca starch, 6 parts of calcium chloride, 16 parts of glycerin, and 30 parts of deionized water respectively by weight, heat and stir until uniform;
[0061] Step 2: After the mixture in step 1 is evenly stirred, add 15 parts of lignocellulose, 16 parts of poplar fiber, 8 parts of eucalyptus fiber, 6 parts of sisal fiber, 9 parts of asparagus fiber, 3 parts of peanut fiber, 2 parts of pineapple leaf fiber, and then stir until evenly;
[0062] Step 3: The material mixed in step 2 is subjected to high-temperature hot-press molding in a mold. The hot-pressing temperature is 85°C, and the hot-pressing pressure is 36MPa. After hot-pressing, it is cooled, and after cooling, it is cut into plates to obtain natural and environmentally friendly plant fibers. sheet.
Embodiment 3
[0064]Step 1: Take 12 parts of gum arabic, 6 parts of konjac gum, 16 parts of tapioca starch, 5 parts of calcium chloride, 14 parts of glycerin, and 35 parts of deionized water respectively by weight, heat and stir until uniform;
[0065] Step 2: After the mixture in step 1 is evenly stirred, add 17 parts of lignocellulose, 15 parts of poplar fiber, 9 parts of eucalyptus fiber, 9 parts of sisal fiber, 5 parts of asparagus fiber, 5 parts of peanut fiber, 3 parts of pineapple leaf fiber, and then stir, and stir evenly;
[0066] Step 3: The material mixed in step 2 is subjected to high-temperature hot-press molding in a mold. The hot-pressing temperature is 95°C, and the hot-pressing pressure is 22MPa. After hot-pressing, it is cooled, and after cooling, it is cut into plates to obtain natural and environmentally friendly plant fibers. sheet.
PUM
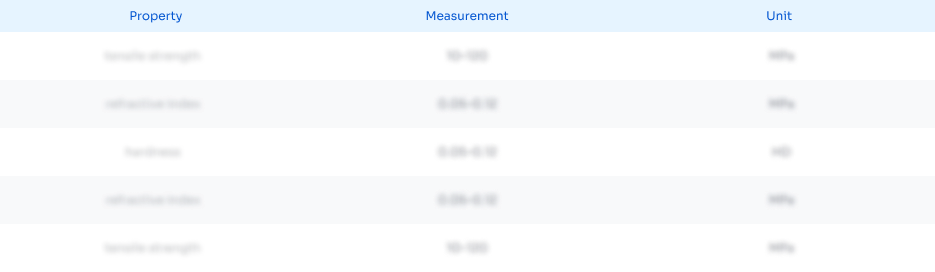
Abstract
Description
Claims
Application Information

- Generate Ideas
- Intellectual Property
- Life Sciences
- Materials
- Tech Scout
- Unparalleled Data Quality
- Higher Quality Content
- 60% Fewer Hallucinations
Browse by: Latest US Patents, China's latest patents, Technical Efficacy Thesaurus, Application Domain, Technology Topic, Popular Technical Reports.
© 2025 PatSnap. All rights reserved.Legal|Privacy policy|Modern Slavery Act Transparency Statement|Sitemap|About US| Contact US: help@patsnap.com