Method for producing glycol dimethyl ether
A technology of ethylene glycol dimethyl ether and ethylene glycol monomethyl ether, applied in the field of preparation of ethylene glycol dimethyl ether, can solve the complex decolorization treatment of sodium chloride, the loss of economic value of sodium chloride, and the inconvenience of production process design. Reasonable and other issues, to achieve the effect of improving the utilization rate of raw materials, reducing the occurrence of side reactions and stable properties
- Summary
- Abstract
- Description
- Claims
- Application Information
AI Technical Summary
Problems solved by technology
Method used
Image
Examples
Embodiment 1
[0019] Put 1Kg of ethylene glycol monomethyl ether liquid into the reaction kettle, then put 0.263Kg caustic soda into the reaction kettle while stirring, and turn on the cooling water of the reaction kettle at the same time, control the temperature in the reaction kettle at 18~19°C, wait for caustic soda When the solid disappears completely, add 0.263Kg of caustic soda again, continue to stir, and control the temperature in the reaction kettle within the range of 27-29°C, and continue to stir for 20 minutes when all caustic soda disappears, so that all components can fully react. Then, slowly feed monochloromethane gas into the reactor to keep the pressure in the reactor at 0.05-0.5 MPa. Since a large amount of heat will be released during the aeration reaction, it is necessary to open a large amount of condensed water to keep the internal temperature of the reactor at 70 ~75°C, ventilation time is 8 hours. After aeration, the mixed liquid was distilled, and the distillate wa...
Embodiment 2
[0021] Put 1.7Kg ethylene glycol monomethyl ether liquid in the reaction kettle, then drop 0.447Kg caustic soda into the reaction kettle while stirring, open the cooling water of the reaction kettle at the same time, control the temperature in the reaction kettle at 18°C, and wait for the caustic soda to solidify When the caustic soda disappears completely, add 0.447Kg of caustic soda again and continue to stir while controlling the temperature in the reaction kettle within the range of 27-28°C. When caustic soda completely disappears, continue to stir for 25 minutes to fully react the components. Then, slowly feed monochloromethane gas into the reactor to keep the pressure in the reactor at 0.05-0.5MPa. Since a large amount of heat will be released during the aeration reaction, it is necessary to open a large amount of condensed water to keep the internal temperature of the reactor at 74 ~75°C, ventilation time is 8 hours. After aeration, the mixed liquid was distilled, and t...
Embodiment 3
[0023] Put 2.3Kg ethylene glycol monomethyl ether liquid into the reaction kettle, then put 0.605Kg caustic soda into the reaction kettle while stirring, turn on the cooling water of the reaction kettle at the same time, control the temperature in the reaction kettle at around 18°C, wait for the caustic soda When the solid disappears completely, add 0.605Kg of caustic soda again and continue to stir while controlling the temperature in the reaction kettle within the range of 27-28°C. When all caustic soda disappears, continue to stir for 30 minutes to fully react the components. Then, slowly feed monochloromethane gas into the reactor to keep the pressure in the reactor at 0.05-0.5MPa. Since a large amount of heat will be released during the aeration reaction, it is necessary to open a large amount of condensed water to keep the internal temperature of the reactor at 73 ~75°C, ventilation time is 8 hours. After aeration, the mixed liquid was distilled, and the distillate was d...
PUM
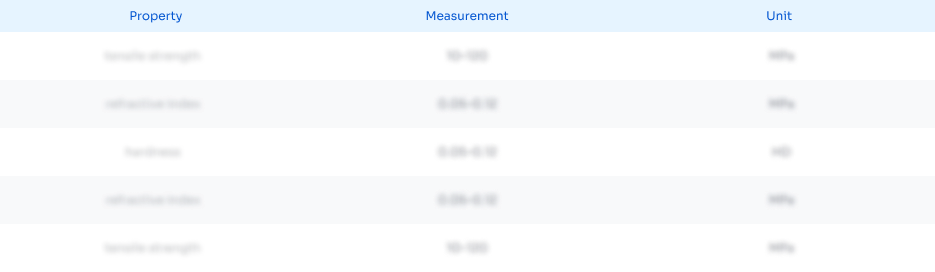
Abstract
Description
Claims
Application Information

- Generate Ideas
- Intellectual Property
- Life Sciences
- Materials
- Tech Scout
- Unparalleled Data Quality
- Higher Quality Content
- 60% Fewer Hallucinations
Browse by: Latest US Patents, China's latest patents, Technical Efficacy Thesaurus, Application Domain, Technology Topic, Popular Technical Reports.
© 2025 PatSnap. All rights reserved.Legal|Privacy policy|Modern Slavery Act Transparency Statement|Sitemap|About US| Contact US: help@patsnap.com