Novel spiral wound krah pipe continuous production technology and device
A technology of spiral winding and production process, which is applied to the continuous production process and equipment field of the new spiral winding carat tube, can solve the problems of unstable product quality, high processing cost and high electrical loss cost, and achieves fast construction connection speed and production quality. Guaranteed effects with different cooling rates
- Summary
- Abstract
- Description
- Claims
- Application Information
AI Technical Summary
Problems solved by technology
Method used
Image
Examples
Embodiment 1
[0043] A new continuous production process of helically wound carat tubes, the detailed steps are:
[0044] The first step is to set the production process temperature of the main engine. The barrel process temperature of the main engine is set to 165°C, and the mold process temperature of the runner machine of the main engine is set to 175°C. The mixing and heating extrusion operations are performed, and the mold of the runner machine is used to Extruded round tube;
[0045] The second step is to start the auxiliary machine to extrude the flat belt, and wrap the flat belt on the forming drum mold to complete the winding of the round tube, and then complete the winding of the socket and the socket. According to different specifications, the width and thickness of the flat belt are inconsistent, and the flat belt The belt mainly plays the role of inner and outer walls during the winding process;
[0046] The third step is to observe whether the product pitch meets the required...
Embodiment 2
[0054] A new continuous production process of helically wound carat tubes, the detailed steps are:
[0055] The first step is to set the production process temperature of the main engine. The barrel process temperature of the main engine is set to 185°C, and the mold process temperature of the runner machine of the main engine is set to 190°C. The mixing and heating extrusion operations are performed, and the mold of the runner machine is used to Extruded round tube;
[0056] The second step is to start the auxiliary machine to extrude the flat belt, and wrap the flat belt on the forming drum mold to complete the winding of the round tube, and then complete the winding of the socket and the socket. According to different specifications, the width and thickness of the flat belt are inconsistent, and the flat belt The belt mainly plays the role of inner and outer walls during the winding process;
[0057] The third step is to observe whether the product pitch meets the required...
Embodiment 3
[0065] A new continuous production process of helically wound carat tubes, the detailed steps are:
[0066] The first step is to set the production process temperature of the main engine. The barrel process temperature of the main engine is set to 178°C, and the runner mold process temperature of the main engine is set to 180°C. The mixing and heating extrusion operations are performed, and the runner machine mold is used to Extruded round tube;
[0067] The second step is to start the auxiliary machine to extrude the flat belt, and wrap the flat belt on the forming drum mold to complete the winding of the round tube, and then complete the winding of the socket and the socket. According to different specifications, the width and thickness of the flat belt are inconsistent, and the flat belt The belt mainly plays the role of inner and outer walls during the winding process;
[0068] The third step is to observe whether the product pitch meets the required product specification...
PUM
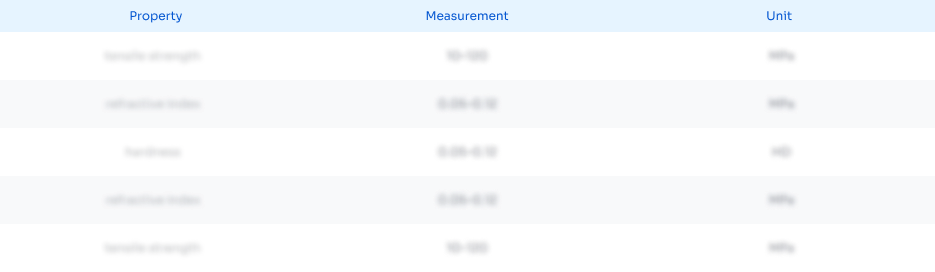
Abstract
Description
Claims
Application Information

- Generate Ideas
- Intellectual Property
- Life Sciences
- Materials
- Tech Scout
- Unparalleled Data Quality
- Higher Quality Content
- 60% Fewer Hallucinations
Browse by: Latest US Patents, China's latest patents, Technical Efficacy Thesaurus, Application Domain, Technology Topic, Popular Technical Reports.
© 2025 PatSnap. All rights reserved.Legal|Privacy policy|Modern Slavery Act Transparency Statement|Sitemap|About US| Contact US: help@patsnap.com