Motor stator and winding method thereof
A winding method and motor technology, applied in the shape/style/structure of winding conductors, magnetic circuit shape/style/structure, magnetic circuit static parts, etc., can solve the problem of large consumables, narrow installation location, and enlarged motor volume and other problems, to achieve the effect of high output power, easy installation and compact structure
- Summary
- Abstract
- Description
- Claims
- Application Information
AI Technical Summary
Problems solved by technology
Method used
Image
Examples
Embodiment 1
[0039] The motor stator provided by this embodiment, such as Figure 1-2 As shown, it includes an iron core 10 and a stator winding 20 wound on the iron core 10 .
[0040] Such as figure 1 As shown, the iron core 10 is equidistantly provided with stator slots 11 of 120 slots, and the shape of the stator slots 11 can be a conventional shape, such as a rectangular slot, and the slot walls of the stator slots 11 of each slot are laid with Matching insulating paper (not shown in the figure), the insulating paper is also the insulating paper used in the conventional motor stator, and will not be described in detail here.
[0041]The stator winding 20 is a three-phase winding matched with the iron core 10, and the number of magnetic pole pairs is four. Each phase of the stator winding 20 includes two groups of stator coil groups wound on the corresponding stator slots 11 on the iron core 10 by means of wave winding, and the two groups of stator coil groups are respectively wound o...
Embodiment 2
[0049] The difference between this embodiment and the first embodiment is that the stator winding 20 of this embodiment is different from that of the first embodiment. In this embodiment, the stator winding is also a three-phase winding, the number of magnetic pole pairs is four, and the winding method of each phase is the same. Each phase of the stator winding 20 includes eight sets of stator coil groups wound in a stacked manner. Each set of stator coil sets is respectively stacked on two sets of stator slot sets separated by ten slots. Each set of stator slot sets includes five slot phases. Adjacent stator slots, the winding direction of each set of stator coil groups is the same, and two adjacent sets of stator coil sets share a set of stator slot sets, except for two sets of adjacent stator coil sets, the adjacent two sets of stator coil sets The coils are connected in series through a group of connecting coils. The two ends of the stator coil group after series connectio...
Embodiment 3
[0057] The difference between this embodiment and Embodiment 2 is that, in this embodiment, the number of stator slots 11 on the iron core 10 is 126 slots, the number of magnetic pole pairs is three, and each phase of the stator winding 20 includes six groups that are wound in a stacked manner. The set stator coil group 21, each group of stator coil groups are stacked on two sets of stator slot groups with fourteen slots at intervals, each group of stator slot groups includes seven adjacent stator slots 11, each group of stator coil groups 21 The winding direction is the same, and the adjacent two sets of stator coil groups 21 share a set of stator slot groups, except for the two adjacent stator coil groups 21, the adjacent two sets of stator coil groups are respectively connected through a set of coils Groups are concatenated end to end.
[0058] The winding method of the stator winding 20 of this implementation is as follows: image 3 As shown, each corresponding electronic...
PUM
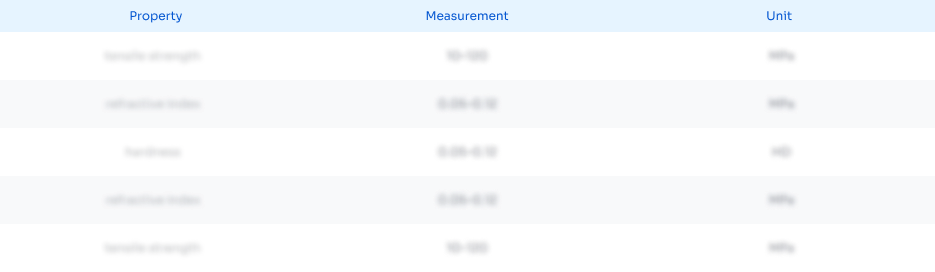
Abstract
Description
Claims
Application Information

- R&D Engineer
- R&D Manager
- IP Professional
- Industry Leading Data Capabilities
- Powerful AI technology
- Patent DNA Extraction
Browse by: Latest US Patents, China's latest patents, Technical Efficacy Thesaurus, Application Domain, Technology Topic, Popular Technical Reports.
© 2024 PatSnap. All rights reserved.Legal|Privacy policy|Modern Slavery Act Transparency Statement|Sitemap|About US| Contact US: help@patsnap.com