Micro-morphology measuring system of XYZ-[beta] dour-dimensional scanning probe
A scanning probe and measurement system technology, applied in the field of microstructure processing and microstructure surface quality detection, can solve the problems of reducing measurement accuracy and measurement reliability, inability to measure, and distorted measurement results, and achieves an increase in the maximum detectable angle. , the effect of reducing sensitive characteristics and strong measurement ability
- Summary
- Abstract
- Description
- Claims
- Application Information
AI Technical Summary
Problems solved by technology
Method used
Image
Examples
Embodiment Construction
[0023] Concrete working process of the present invention can be through the attached figure 2 , image 3 and Figure 4 The example is described in detail.
[0024] When the system starts to work, the measured sample (8) is placed on the XYZ-β four-dimensional scanning module, and the relative position of the sample (8) and the probe (9) is adjusted through the translational movement of the four-dimensional scanning module, so that the probe (9) In contact with the smooth area of the surface of the sample (8). After the contact is determined, driven by the XYZ-β four-dimensional scanning module, the sample (8) is first linearly scanned along the horizontal direction, such as figure 2 As shown, the microprobe module will sequentially detect the surface topography changes on the sample (8).
[0025] figure 2 In scanning P 0 -P 1 Point, P 3 -P 4 Point and P 6 -P 7 In the smooth area between points, the inclination angle of the surface profile of the scanned area is...
PUM
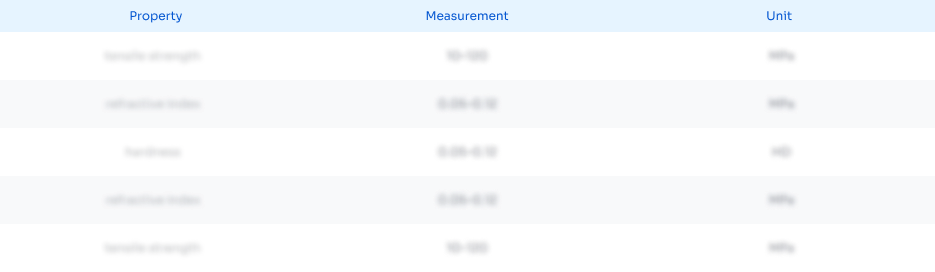
Abstract
Description
Claims
Application Information

- R&D Engineer
- R&D Manager
- IP Professional
- Industry Leading Data Capabilities
- Powerful AI technology
- Patent DNA Extraction
Browse by: Latest US Patents, China's latest patents, Technical Efficacy Thesaurus, Application Domain, Technology Topic, Popular Technical Reports.
© 2024 PatSnap. All rights reserved.Legal|Privacy policy|Modern Slavery Act Transparency Statement|Sitemap|About US| Contact US: help@patsnap.com