Production process of water-resistant coating composition for buses
A production process and composition technology, applied in the direction of polyurea/polyurethane coatings, coatings, etc., can solve problems such as insufficient water resistance, and achieve the effect of avoiding electrical short circuit and improving safety performance.
- Summary
- Abstract
- Description
- Claims
- Application Information
AI Technical Summary
Problems solved by technology
Method used
Examples
Embodiment 1
[0010] Put 21 parts of modified polyurethane resin emulsion and 21 parts of modified diphenylmethane diisocyanate into the reaction kettle and mix them. The mixing time is 1h, the mixing temperature is 50 degrees, and the mixing speed is 120r / min. After mixing, add 12 parts Dispersant, continue to stir for 30 minutes, then add 7 parts of talcum powder, 10 parts of kaolin and 5 parts of titanium dioxide, the mixing temperature is 60 degrees, the mixing speed is 140r / min, until the mixture is uniform, then naturally cool to room temperature.
Embodiment 2
[0012] Put 35 parts of modified polyurethane resin emulsion and 35 parts of modified diphenylmethane diisocyanate into the reaction kettle and mix them. The mixing time is 1.5h, the mixing temperature is 60 degrees, and the mixing speed is 120r / min. After mixing, add 22 1 part of dispersant, continue to stir for 30 minutes, then add 10 parts of talc powder, 9 parts of kaolin and 5 parts of titanium dioxide, the mixing temperature is 65 degrees, the mixing speed is 140r / min, until the mixture is uniform, then naturally cool to room temperature.
Embodiment 3
[0014] Put 25 parts of modified polyurethane resin emulsion and 15 parts of modified diphenylmethane diisocyanate into the reactor and mix them. The mixing time is 2 hours, the mixing temperature is 55 degrees, and the mixing speed is 140 r / min. After mixing, add 9 parts Calcium stearate, continue to stir for 30 minutes, then add 3 parts of talcum powder, 2 parts of kaolin and 1 part of titanium dioxide, the mixing temperature is 65 degrees, the mixing speed is 130r / min, until the mixing is uniform, then naturally cool to room temperature.
[0015] Beneficial effects: the present invention adopts a new formula and unique formula components to achieve effective waterproofing, and the water-resistant coating composition prepared by the present invention can effectively prevent water from penetrating into the inner end of the busway, avoid electrical short circuit, and cause busbar explosions , improve safety performance.
PUM
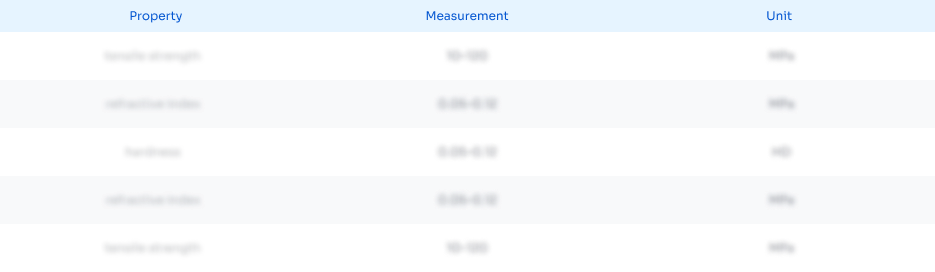
Abstract
Description
Claims
Application Information

- R&D Engineer
- R&D Manager
- IP Professional
- Industry Leading Data Capabilities
- Powerful AI technology
- Patent DNA Extraction
Browse by: Latest US Patents, China's latest patents, Technical Efficacy Thesaurus, Application Domain, Technology Topic, Popular Technical Reports.
© 2024 PatSnap. All rights reserved.Legal|Privacy policy|Modern Slavery Act Transparency Statement|Sitemap|About US| Contact US: help@patsnap.com